Production Split-O-Matic Splitters accurately divide large volumes of bulk sample material through three or five stages in a single pass. The unique design adapts to a wide variety of applications and sampling environments. Our most popular Production Split-O-Matic models are listed, but custom modifications are available for installation in production or pilot-plant facilities.
Production Split-O-Matics have chute widths from 0.5–12in (13–305mm) and three or five stages of riffle chutes. Three-stage models feature selectable final sample fractions of 1/2, 1/4, or 1/8, using adjustable fraction control gates to regulate material flow. Five-stage units yield a single 1/32 fraction size and are non-adjustable. Standard V-bottom chutes are sloped at 45° and precisely align material flow for more accurate divisions. Rugged, heavy steel construction throughout assures long service life.
Custom design options include models with an alternate number of dividing stages, 60° slopes for low-density materials, fabrication with all stainless steel contact parts, custom-sized material hoppers, fixtures for installations integrated with existing equipment, and special collection pans. Pneumatic operation for hopper and fraction gates is standard for SM-1A and SM-2A, our two largest models. It is also a convenient custom option on models with chute widths of 4in (102mm) or less.
Material Hoppers with capacities from 1.6 to 12ft³ (45 to 340L) and sample pans are sold separately for design flexibility. Bulk material is accumulated in hoppers before releasing into the chutes, assuring a consistent flow of material across the entire width of chutes for even divisions. Recommended standard hopper sizes for the Split-O-Matic assemblies are indicated in the chart.
The usable particle size range for Production Split-O-Matics is from 5in (127mm) to fine sand. Chute widths should be a minimum of two times the largest particle size to avoid bridging. For oblong shapes or low-density materials such as coal or coke, three to four times the top size is recommended.
Note: Material Hoppers and Sample Pans are sold separately for design flexibility.
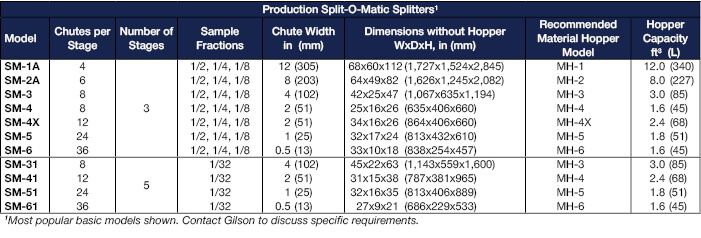
Click the Comparison Table above to enlarge, print, or download.
Contact us to discuss custom designs for your application:
- 60° chute slopes for low-density materials
- Alternate numbers of splitting stages
- Fabrication with all stainless steel contact parts
- Specially-sized material hoppers
- Pneumatically operated hopper gates and fraction gates
- Installation fixtures
- Special collection pans
Features:
- Fast, accurate separations of large sample volumes in production or pilot-plant facilities
- Efficiently divides test samples in just one pass
- Models with fraction control gates regulate the final fraction
- V-bottom chutes precisely align material flow for accurate divisions
Included Items:
- Production Split-O-Matic Splitter
Accessories:
Related blogs: