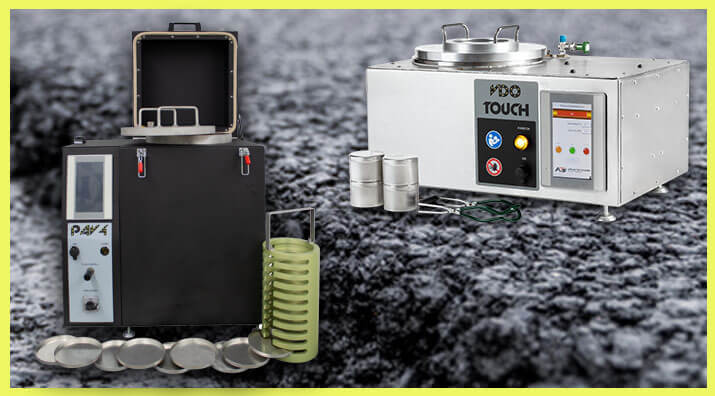
The adoption of Superpave methods for asphalt mix design brought about many new tests to examine and characterize asphalt binders. Pavement designers and asphalt producers recognized that the properties and durability of asphalt mixes changed over time as the binder aged, and a method was needed to predict how pavements would behave over the long term.
The Pressure Aging Vessel (PAV) was developed to artificially age asphalt binders, allowing testing of the aged material to predict future performance. Vacuum Degassing Ovens (VDOs) remove entrapped air from processed PAV samples to ensure accurate test results. This blog post maps out the background, procedures, and equipment associated with the simulated aging of asphalt binders.
Background
Oxidative aging changes the rheological properties of asphalt binders over time, significantly impacting the long-term performance of pavements and sometimes resulting in premature deterioration and cracking. As oxygen slowly alters binder properties, the asphalt binder stiffens, leading to fatigue cracking, low-temperature cracking, and other pavement distress.
The Pressure Aging Vessel (PAV) uses heat and pressure to artificially age asphalt binder samples, reproducing the effects of in-service aging over a 7 to 10-year period. The process does not produce test results but prepares the binder material for testing to establish its performance grade properties noted in ASTM D6373 or AASHTO M 320. Additional Tests performed with the aged samples include:
Dynamic Shear Rheometer (DSR) determines resistance to damage from age, temperature, and mechanical forces over a wide temperature range. ASTM D7175, AASHTO T 315.
Bending Beam Rheometer (BBR) determines flexural creep stiffness. ASTM D6648, AASHTO T 313.
The Direct Tension (DT) test determines low-temperature fracture properties. AASHTO T 314.
The ability to mimic the properties of aged binder and compare results between aged and unaged samples enables these tests to anticipate future pavement performance reliably. Understanding how in-service aging affects resistance to fatigue and low-temperature cracking leads to better predictions of binder-related pavement distress and promotes better and longer-lasting asphalt pavements.
The conditioning process follows the standard practices in ASTM D6521 and AASHTO R 28. PAV conditioning equipment allows testing laboratories to provide a complete range of asphalt testing services for their clients, ensuring accurate in-house test results with no need to outsource.
Short-term aging also affects binder performance and is the result from exposure to heat and air during asphalt mix production and pavement placement. The effects of short-term aging are simulated in the laboratory with the Rolling Thin Film Oven (RTFO) using ASTM D2872 and AASHTO T 240 standard test methods. PAV samples to be tested as Superpave performance-graded binders are obtained from binder residue aged in the RTFO.
Sample Preparation
Samples to be conditioned in the Pressure Aging Vessel are recovered from RTFO bottles after short-term aging in the Rolling Thin Film Oven. The binder sample is transferred into a single container and thoroughly mixed to ensure homogeneity.
The PAV is preheated between 90° and 110°C (194° and 230°F), depending on binder grading and the climate environment. Exact temperature requirements are found in ASTM D6373 or AASHTO M 320 standard specifications for performance-graded binder. The asphalt binder material is poured into individual PAV sample pans, and the pans are placed in a holder for loading into the PAV.
Oxidative Aging Simulation
Once the prepared samples are loaded in the PAV, the chamber lid is closed, and its bolts are tightened sequentially with a torque wrench to the manufacturer’s specifications. After the chamber temperature recovers to the specified setpoint, a pressure of 2.1MPa (305psi) is applied. This pressure and the specified temperature are maintained for 20 hours. Depressurization at completion is performed slowly to avoid bubbling and foaming in the samples and takes about 8 to 15 minutes.
Vacuum Degassing
The samples are recovered from the chamber and transferred to a separate warming oven for 15 minutes. The binder samples may still contain some air, which affects post-aging tests. Contents of all the PAV pans containing the same sample are transferred to a single container for processing in a Vacuum Degassing Oven (VDO) to remove any remaining entrapped air. The PAV samples are now ready for further tests that characterize the properties of the aged binder.
Testing Equipment
Gilson recommends our Pressure Aging Vessel (PAV4) and Vacuum Degassing Oven (VDO) for simulated long-term aging of asphalt binders.
The PAV meets ASTM, AASHTO, and EN requirements and completes the binder aging cycle in three easy steps:
- Press the heat button
- Insert the specimens when prompted
- Press the age button
A touch-screen controller with integrated operating software regulates and monitors all processes, and a battery backup ensures uninterrupted operation. Processing data is logged and downloadable via a USB port. The platinum RTD device ensures temperature accuracy and uniformity. Integral thermal shut-down and pressure relief devices allow safe operation.
Gilson’s VDO models feature fully automated operation for degassing of PAV samples and meets ASTM, AASHTO, and EN specifications. The industrial-grade touch-screen controller of the VDO Touch is menu-driven, and the unit has programmable temperature set points, soak times, and vacuum levels.
We hope this blog has helped you understand the function of PAVs and VDOs for aging asphalt binder samples. Please contact the testing experts at Gilson for help with your applications.
Testing Resources
Standard Test Methods, Specifications, and Practices
Individual test methods and specifications referenced in our product descriptions, blog articles, and videos are available for review or purchase from the professional organizations noted.
- ASTM International (American Society for Testing and Materials)
- AASHTO (American Association of State Highway and Transportation Officials)
- ACI (American Concrete Institute)
- State DOTs (Departments of Transportation)
- ISO (International Organization for Standardization)
- BS (British Standards)
- EN (European Standards)