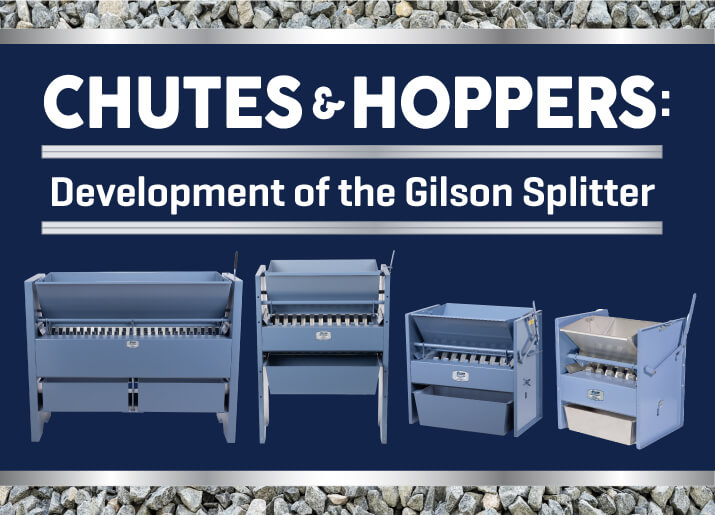
It was the mid-1950s, and highway construction in the United States was booming. Thought leaders in the construction materials testing industry were waking up to the benefits of quality control practices and standardization of test methods. Our Testing Screen was gaining popularity as a valuable tool for maintaining standards, and Gilson was looking for more ways to meet the needs of loyal customers.
Increasing awareness of the influence of aggregate characteristics on concrete mix designs and asphalt paving materials spurred the development of ASTM and AASHTO standard test methods for better classification of the size and shape of aggregate particles. Before these tests could be useful, there needed to be some assurance that the test samples accurately represented the bulk material and that the tests themselves were accurate.
Outdated Designs for Modern Problems?
People in the aggregate testing industry have never been strangers to the principles of representative sampling. Still, there was a lack of innovative and efficient equipment to execute the simple task of sample dividing. Riffle splitters were popular but had limitations. These devices have a series of chutes that quickly divide granular materials into two halves.
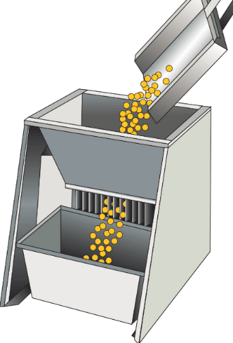
Riffle splitters work well when properly matched to a narrow range of particle sizes, but in the real world, size specifications for aggregate blends vary widely.
A splitter built with fixed 1in wide chutes will not accurately divide 1in or even 3/4in particles. The particles will not be distributed evenly over the chute openings, and many will jam together, or “bridge” with one another and block the openings.
Conversely, a 4in wide chute is not optimum for splitting sand-sized materials. The ideal width for a chute is around two to three times greater than the maximum particle size. Testing agencies and labs found themselves faced with buying multiple pieces of equipment just to stay current with specification requirements.
There are other problems with the conventional riffle splitter design as well. They rely upon the user to distribute the bulk sample evenly across the width of the chutes. The open hopper is nothing more than a funnel, directing any stray material toward the chute openings. Most of the sample ends up being deposited over the center 1/3 or ½ of the total span of the chutes, resulting in poorly divided samples that do not represent the whole.
Turning Ideas into Solutions
The product designers at Gilson saw problems that they could solve with innovation rather than by just producing multiple units, and stepped in with a concept that became known as the Universal Splitter.
The first step in rethinking was to find a way to adjust chute widths for multiple aggregate blends with different gradations and maximum sizes. This flexibility would allow the user to optimize one device to process many different samples.
The Gilson solution was to assemble a series of square aluminum or stainless-steel bars to pivot around a steel rod. Installing this assembly parallel with the hopper opening meant they could flip an even number of bars to either side to produce V-shaped chutes of nearly any width they wanted. Tightening wingnuts at either end of the threaded rod drew the bars together to form nearly seamless surfaces of the correct width for the size, shape, and texture of the bulk sample particles. The number of bars selected to distribute evenly on each side controls the chute width and optimizes the splitter for the characteristics of each sample material.
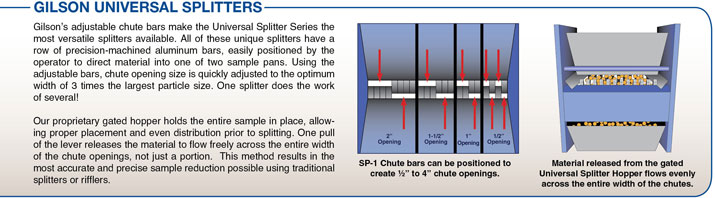
The designers then moved on to the problem of uneven distribution when the material is introduced into the splitter. Typically, the operator collects a randomly distributed scoop of the bulk material and manually pours it through the splitter chutes. Even when performing this step carefully, the flow of material is erratic and not directed across the entire span of the chutes.
The solution here was to place the material in a closed hopper, so the operator can take a few seconds to arrange the material evenly. The simple mechanical linkage opens the clamshell-design hopper and directs the sample flow equally across the entire width of the chutes. The speed and volume of flow are regulated, and the sample is deposited over the whole width of the chutes, ensuring a uniform split.
Building on a Theme
So, innovative design now meant that our customers could use one instrument instead of several for a variety of material types while producing representative samples more efficiently. It’s easy to understand why there have been so few design changes over the years. The models introduced after the original model SP-1 design built on the already wide range of sizes and volumes and added convenient benchtop models.
The suggested size ranges for our Universal Splitters are based on a conservative recommendation for openings approximately three times the maximum particle size. The added width allows accurate splitting for materials that may have some flat and elongated particles or angular surfaces. Free-flowing materials may be divided reliably with chute widths from 2 to 2.5 times greater than maximum particle size. ASTM C702/AASHTO R 76 standard practices require chutes to be at least 50% (1.5 times) wider than the largest particle.
Universal Splitter Models
The Universal Splitter series features models all based on the simple design of adjustable-width chutes and a lever-release hopper.
- SP-0 meets the demand for a Universal splitter for high-volume samples with large maximum particle sizes. 4in to 6in maximum particle sizes are split equally into four different sample pans in one pass.
- SP-1 was the first Universal splitter and is still the most versatile. This splitter was built to process the most common coarse aggregate blends and adapts easily for fine and coarse sizes across the spectrum. Accessories are available to collect bagged samples and control dust output. And optional wheels increase mobility.
- SP-2 has plenty of capacity to handle most coarse aggregate sizes but is compact enough to be positioned on the floor or a benchtop. Ideal for many fine and coarse aggregate blends.
- SP-2.5 is compact, easily portable, and ideal for fine aggregate sizes, and a dust enclosure accessory reduces nuisance dust in operation.
- SP-3 and SP-33 Universal Mini-Splitters are an extension of the Universal design for powders and fine granular materials.
Model | Maximum Particle Size, in (mm) | Hopper Capacity, ft³ (L) | Chute Bar Size, in (mm) | Number of Chute Bars |
---|---|---|---|---|
SP-0 | 4–6 (102–152) | 3.5 (99) | 1 (25) | 48 |
SP-1 | 2–3 (51–76) | 1 (28) | 0.5 (13) | 48 |
SP-2 | 1.5–2 (38–51) | 0.55 (15.6) | 0.5 (13) | 36 |
SP-2.5 | 1–1.5 (38–51) | 0.28 (7.9) | 0.25 (6) | 48 |
SP-3 | 0.25 (6.4) | 0.6 (1.7) | 0.125 (3) | 48 |
SP-33 | 0.25 (6.4) | 0.6 (1.7) | 0.125 (3) | 48 |
Gilson Videos
Gilson’s Video Library has an extensive selection of videos with product features, testing tips, and do-it-yourself guidance for our products. Listed below are links to some of the most helpful videos for selecting and using Gilson Universal Splitters.
Universal Splitters
- SP-0, 3.5ft³ (99.1L), 4in (102mm) Maximum Particle Size
- SP-1, 1.0ft³ (28.3L), 2in (51mm) Maximum Particle Size
- SP-2.5, 0.28ft³ (7.9L), 1in (25mm) Maximum Particle Size
Universal Mini-Splitters
Helpful Sample Splitting Videos
- Gilson Tips for Sample Dividing Aggregates
- Reducing Aggregate Samples to Testing Size, ASTM C702, AASHTO T 248
- Reducing Fine Aggregate Samples, ASTM C702, AASHTO T 248
An Overview of Gilson Splitters
We hope this blog post has been informative and helped you make decisions in selecting your sampling and dividing equipment. Please contact the Testing Experts at Gilson to discuss your application.
Testing Resources
Standard Test Methods, Specifications, and Practices
Individual test methods and specifications referenced in our product descriptions, blog articles, and videos are available for review or purchase from the professional organizations noted.
- ASTM International (American Society for Testing and Materials)
- AASHTO (American Association of State Highway and Transportation Officials)
- ACI (American Concrete Institute)
- State DOTs (Departments of Transportation)
- ISO (International Organization for Standardization)
- BS (British Standards)
- EN (European Standards)