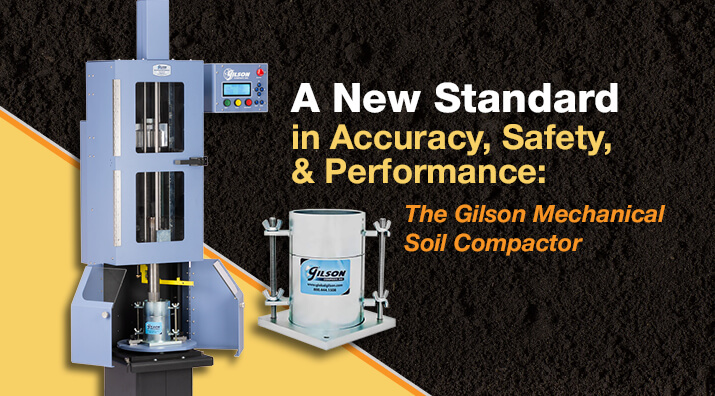
Those of us who have worked in the soils section of a construction materials testing laboratory may remember the moisture-density relationship of soils, or the Proctor test, as one of the first test methods we trained on. The concept of soil compaction and the test itself are easily understood and following each individual step in the process develops the trainee's attention to detail.
But let's be honest, the new person usually gets the assignment because it's tedious and physical, and no one else wants to do it. Proctor Compaction Test: A Basic Guide is a previous Gilson blog article addressing the basics of Proctor test methods and explaining the required equipment.
The modified Proctor test calls for repeatedly lifting a 10lb (4.5kg) sliding drop hammer 18in (46cm) high and releasing it. When performed by one person with manual equipment, the effort is physically demanding. The most extreme version of this test specifies five soil layers, each compacted with 56 hammer blows, so you can skip arm day at the gym. Standard Proctors are a bit easier physically, but for any of the methods, miscounted blows and incomplete drop heights common when using a manual hammer and are significant human errors responsible for inaccurate and inconsistent test results.
Early Mechanical Soil Compactors: An Imperfect Solution
Mechanical soil compactors have been around for a long time and have resolved many of these issues. Still, these machines have always had issues of their own. Outdated designs lead to unreliable operation and breakdowns. Their mechanical assemblies often drift out of tolerance and require frequent readjustment.
Although numerous soil test methods rely on similar methods of compacting soil materials into molds, some mechanical compactors can be used only for a narrow range of applications. Others only accept soil compaction molds from a particular manufacturer. Design, operational, or ergonomic issues that make the equipment difficult to use are still common.
Gilson's new mechanical soil compactor resolves these issues by meeting them head-on, using thoughtful design, innovative technology, and quality materials and components. This blog article takes a close look at the compactor and its features.
Gilson and the Modern Mechanical Soil Compactor
Soil compactors from different manufacturers have been used for many years. Still, the design and features of most models have hardly changed at all in this time. Manufacturers have been slow to consider improvements in performance updates that keep pace with available technology.
Gilson listens to our customers, and they have made it clear that accuracy, safety, and versatility are their priorities for all construction materials testing equipment, including soil compactors. This user feedback provides direction and helps us set goals for the progressive design of next-generation testing devices.
The Gilson Mechanical Soil Compactor grew out of a collaboration between Gilson's experienced technical staff and our forward-looking engineering team to develop a new compactor that belongs in a modern soils lab. We believe that innovation creates better products, better results, safe, efficient operation, and greater versatility.
Accuracy & Repeatability
The accuracy of the Proctor moisture/density test is based on more than just the hammer weight and drop height. Human error can include miscounted hammer drops, inconsistent drop height caused by fatigue, and even using the wrong mold size or hammer weight for the selected test method. The Gilson Compactor is designed and built to minimize human error and comply with a variety of test method specifications.
- The Gilson Soil Compactor is factory calibrated before shipping. Calibration should be performed annually or at intervals not exceeding 1,000 tests. The ASTM D2168 calibration procedure can be performed at any time to verify the accuracy and performance of any mechanical compactor using the Compactor Calibration Kit from Gilson.
- Pre-programmed ASTM and AASHTO test methods in the drop-down menu of the digital controller show individual requirements for mold size, drop height, number of sample layers, and number of hammer blows, minimizing operator input errors.
- Optical thru-beam sensors control the hammer mechanism, counting actual hammer blows instead of cycles of the mechanism. The programmed number of hammer blows is delivered to the soil sample every time, and hammer drop heights automatically adjust relative to the surface of the soil sample.
- Indexed rotation of the turntable is calculated for different test methods and mold sizes and programmed into the servo motor. Hammer blows are distributed evenly for each soil lift and every compaction cycle, regardless of test type.
- The current lift (soil layer) and the number of hammer blows are continuously shown on the digital controller's four-line LCD display and updated in real time during the test cycle.
- A pause feature allows the compaction to be suspended in mid-cycle in case the addition of soil is required or other adjustments must be made. Operation continues from the accumulated blow count when resumed.
Versatility & Customization
Compacting a soil sample into a mold with a drop hammer is a familiar method used for a variety of tests to regulate the compactive effort applied to a controlled sample volume. The technique produces reliable results for moisture/density relationship (Proctor) tests and offers consistent sample preparation for California and Limerock bearing (CBR or LBR) tests, soil-cement/soil-lime strength tests, and soil permeability tests.
Molds and compaction routines for the different tests are similar but not exactly the same. Conventional soil compactors often cannot overcome minor obstacles like differences in mold and collar dimensions or the configuration of the hammer face.
- Gilson's Mechanical Compactor is adaptable to meet the requirements of a variety of soil compaction test methods:
Test Methods Compatible with the Gilson Soil Compactor Standard Test Method ASTM AASHTO Soil Moisture-Density (Proctor) D698, D1557 T 99, T 180 California Bearing Ratio (CBR) D1883 T 193 Limerock Bearing Ratio (LBR) FM 5-515 — Moisture-Density of Soil-Cement D558, D559, D560 T 134, T 135, T 136 Strength of Soil-Lime Moistures — T 220 Soil Hydraulic Conductivity (Permeability) D5856 — - The Gilson Compactor is compatible with ASTM or AASHTO-compliant soil compaction Proctor molds from Gilson or other manufacturers that feature an alignment hole in the center of the base plate.
- The digital controller is programmable to customize the number of blows per lift, the number of lifts in a test cycle, and the indexing angle for the turntable for special compaction and remolding applications.
- 12in or 18in hammer drop heights are selectable in seconds simply by tightening or loosening two knobs.
- A surcharge mass quickly bolts in to change the drop hammer weight from 5.5lb (2.495kg) to 10.0lb (4.536kg).
- Each hammer weight configuration uses a unique top cap, allowing instant visual verification during operation.
Safety & Efficiency
Any machine that automates a physically demanding process is a positive step toward efficient operation and worker safety. Gilson's design makes it possible to meet higher production demands while using safer practices.
- The hammer lift mechanism is enclosed by steel doors with plexiglass windows that allow observation of drop height during operation. The compactor will not operate when the cabinet doors are open.
- A large emergency stop (E-Stop) button positioned on the controller instantly stops operation when pressed.
- A solid steel bar swings into place under the hammer mechanism when changing molds, adding soil, or performing maintenance on the compactor.
- Optional steel Lower Safety Doors with Lexan windows are available to completely enclose the mold platform and indexing table.
- Adjustment for chain drive tension is made from the outside of the cabinet, ensuring safe maintenance for optimum performance.
Ruggedness & Reliability
For laboratory equipment to be cost-effective, it must stand up to hard daily use in a punishing environment. Building a robust and reliable compactor was high on the list of priorities for our design team. In-house machine design and selection of components were heavily biased toward durability and higher capacity.
- The powerful 1/3hp main motor that runs the chain drive lift system is rated for continuous operation.
- The duty-rated servo motor for turntable rotation uses programmable closed-loop position control for precision indexing of the mold.
- Two heavy-duty worm gear reduction drives transfer power to the hammer lift and turntable drives.
- The hammer lift and turntable mechanisms, controller, and digital display are housed in heavy-gauge steel enclosures, and the turntable assembly withstands impact forces greater than 14,000lbf (63kN).
- Heavy steel welded and bolted construction with a durable powder coat finish provides long-lasting durability under rough use.
- Cabinet viewing windows are tough, impact-resistant Lexan polycarbonate.
- Extensive performance testing and evaluation at a major commercial construction materials testing lab in the Midwest confirms the accuracy and reliability of the compactor.
Ergonomics & Convenience
Gilson's Soil Compactor is designed from the ground up for simplicity and ease of use. Reducing the time and effort required for operation and changeover adds value and optimizes efficiency in the lab.
- The mold turntable has a homing feature for automatic return to the start position after each compaction cycle.
- The HMI (Human/Machine Interface) mounts in one of four positions for optimum viewing and easy operation.
- Hinges for the safety door assembly are mounted on either side of the compactor to change the opening direction.
- Solid steel mounting base is predrilled for multiple floor mounting options.
- The optional Base Extension Accessory raises the working height of the compactor.
- Cabinet viewing windows are tough, impact-resistant Lexan polycarbonate.
- Two hammer faces are included with the compactor. A round 2in (50.8mm) diameter face is used for 4in (101.6mm) molds, and the sector (pie-shaped) face is used with 6in (152.4mm) molds.
We hope this article has helped you understand the advantages of the new Gilson Mechanical Soil Compactor Please contact our testing experts for questions or help with your application.
Testing Resources
Standard Test Methods, Specifications, and Practices
Individual test methods and specifications referenced in our product descriptions, blog articles, and videos are available for review or purchase from the professional organizations noted.
- ASTM International (American Society for Testing and Materials)
- AASHTO (American Association of State Highway and Transportation Officials)
- ACI (American Concrete Institute)
- State DOTs (Departments of Transportation)
- ISO (International Organization for Standardization)
- BS (British Standards)
- EN (European Standards)