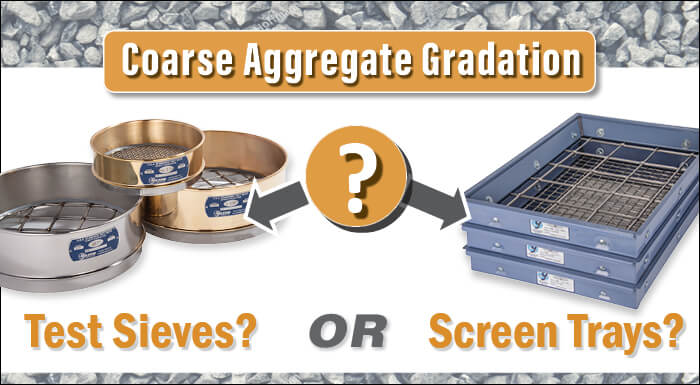
A question we sometimes hear from our customers involves the sieve analysis of coarse aggregate samples with large particle sizes. “Is it necessary to use a testing screen with larger screen trays, or can I use conventional round test sieves?” Like many things, it kind of depends. There is no clearly specified boundary for selecting either type of equipment, but looking at some practical limitations and levels of effectiveness might help.
Aggregate Sample Requirements
ASTM C136 / AASHTO T 27 is the test method used for the sieve analysis of construction aggregates and specifies the mass of the sample to be tested based on the maximum particle size. This same standard also limits the maximum quantity of material retained on each sieve to enable adequate separation and avoid damage to the sieve mesh.
The table below shows sample masses required for various top sizes as well as weight limits for the retained fractions on individual sieves. Remember the retained values are maximum weights and are not always ideal for good separations. It may be more helpful to look at the volume of each fraction and how much space they occupy over the surface area of each sieve.
To judge whether a sieve is overloaded, a rule of thumb endorsed in ASTM Manual 32 “Test Sieving Methods” is that there should be no more than one or two layers of particles remaining on the mesh surface at completion of agitation. Having too many layers increases the possibility that not every particle will be tried to a sieve aperture during the test. Separation may not be complete, and the mesh apertures may be “blinded” or blocked with sample particles.
When sieves are stacked for agitation, either manually or in a sieve shaker, the vertical height of the sieve frame becomes another limiting factor. Stacked test sieves have a limited amount of clearance between their mesh surface and the bottom of the mesh for the sieve above. For proper separation, each particle must have enough space to move freely during agitation, so when it lifts off the screen, it is reoriented to the mesh when it lands again.
As an example, let’s say you have a coarse aggregate gradation sample with a 50mm (2in) top size, and you want to run it on 8in diameter sieves because that’s what is available at the moment. The total mass of the sample would be a minimum of 20kg (44lb). The permissible loading for just the top sieve is 3.6kg or about 13.5% of the total, so this seems like it might work. Well, it probably could, but it may not be all that easy.
Practical Limitations
If the actual amount retained on the 2in sieve is close to the 3.6kg weight limit, there will be too many particles in such a limited surface area to allow a good separation. There will also be clearance issues with the larger aggregate sizes if the sieves are stacked. Each sieve in the stack will only have about 2in of clearance between the wire mesh surface, and if the largest particles are about 2in, they’ll have no room to move during agitation. The C136 test method permits the use of these sieves, but each particle must be tried manually to the sieve apertures.
Workaround Solutions
At this point, if you still want to use those 8in sieves, you still have some options that are allowed in the specification:
- If the frame height of the sieves is too short for the particles to move freely during agitation, or if there are fewer than five full openings in a sieve, you can hand sieve them by manually trying each particle to a sieve opening. Although the test method allows it, this is labor-intensive and dramatically reduces accuracy.
- For samples that overload multiple sieves, you can divide them into two or more roughly equal amounts and sieve each portion. Fraction weights must be combined later for final gradation calculations. That means you are running two or more sieve tests for each gradation, plus splitting samples and performing added calculations.
- If one or two sieves are overloaded, you can try inserting a slightly larger sieve above to intercept some of the larger particles. Material retained on the larger sieve can then be added to the retained mass of the overloaded sieve when weighing. If the addition of a sieve makes the stack too tall to fit into the sieve shaker, you may have to divide the sample into two portions, as noted above.
So, there are ways to get the job done with traditional round sieves, and if you’re in a bind, you may have to exercise one or more of these options. You could also gain some efficiencies by using test sieves with larger frames if your sieve shakers will accept them. But clearly, if you are testing samples like this regularly, a testing screen designed for larger batches of material with larger particle sizes will increase the productivity and efficiency of your testing lab and ensure more accurate and repeatable results.
Testing Screens and Test-Master units are designed primarily for particle sizes from 4in to No. 4 (100mm to 4.75mm). By adjusting agitation times, they can provide reliable results for sizes down to 75µm (No.200). Models are available to hold from five to seven screen trays with a clear screen area of 14.75x22.75in (375x578mm).
Porta-Screen models are more compact, portable, and designed for best performance in the range of 2in (50.8mm) to No. 16 (1.18mm). Units have a total sample capacity of up to 60lb (27kg) and are available to hold up to seven screen trays with a 14x14in (356x356mm) screen area.
Gilso-Matic Screening Assemblies are designed for large-scale production testing of sample batches up to 3ft³ (85L) for particle sizes up to 6in (150mm). Agitation is similar to Testing Screens, but these units feature pneumatic controls to discharge material from screen trays to collection chutes or directly to a platform balance. An optional hopper/feeder assembly dispenses sample materials in batches to the screening assembly. Mounted screen decks have a 24in (610mm) square mesh area.
Continuous-Flow Screens may be an option for scalping large particles from bulk samples or monitoring of continuous feed production. They use one or two front-discharge screen trays and feature adjustable inclined operation for constant throughput. Adjusting the incline of the machine to zero allows limited particle size testing.
We hope this blog post will help you decide on the best equipment and methods for gradation testing of coarse aggregate samples. For expert help with your application, contact the testing experts at Gilson.
Testing Resources
Standard Test Methods, Specifications, and Practices
Individual test methods and specifications referenced in our product descriptions, blog articles, and videos are available for review or purchase from the professional organizations noted.
- ASTM International (American Society for Testing and Materials)
- AASHTO (American Association of State Highway and Transportation Officials)
- ACI (American Concrete Institute)
- State DOTs (Departments of Transportation)
- ISO (International Organization for Standardization)
- BS (British Standards)
- EN (European Standards)