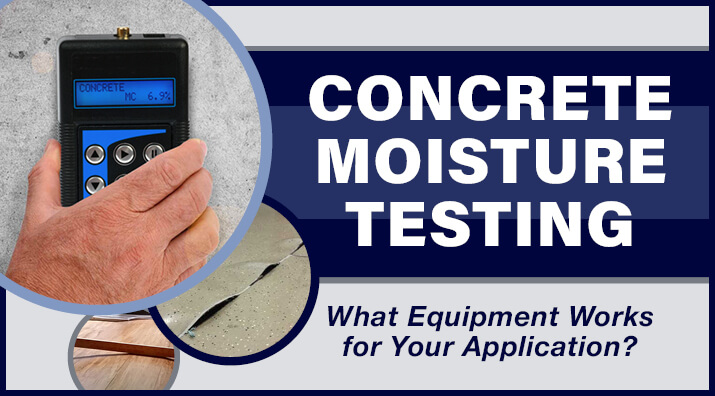
Concrete is easily the most versatile construction material in history, but it presents some unique problems when used in combination with other materials, especially floor coverings. Concrete moisture is always present to some degree in concrete slabs, whether they are suspended in a structure or placed on grade.
If the exposed concrete surfaces are coated with paints, sealants, adhesives, overlaid with tile, or other floor coverings, migrating moisture could cause significant damage. The amount, type, location, and movements of moisture in a concrete slab need to be clearly understood to avoid problems when placing a flooring system over it.
Moisture in Concrete: Sources and Movement
Excess moisture in concrete slabs must reach the surface and evaporate for drying to take place. After the concrete is placed, and while still in a plastic state, small capillaries develop as bleed water is displaced by the settlement of solids and forced to the surface. When the concrete hardens, moisture will still follow these pathways for as long as they remain open. Anything from too much troweling during finishing applications to early applications of curing compounds will slow down or stop this process. Ambient temperatures and humidity also affect drying times.
There are no consistently reliable formulas to accurately predict drying times or moisture content and movement in a concrete slab. Even an older slab may have enough moisture present to damage new coating and flooring overlays. Modern adhesives and coatings manufactured with lower volatile organic compounds (VOCs) may be more susceptible to the effects of moisture than older compounds. It is possible that the moisture levels in an old slab were acceptable with old-style flooring materials, but could cause problems when new products are applied.
- Water is a significant ingredient in all concrete mixes and, in theory, is consumed over time by the hydration process. Free moisture can remain in concrete that has not completely hydrated. Hydration can also be slowed or interrupted by environmental factors, concrete admixtures, or even placement and finishing/troweling practices.
- An existing slab may be retaining water from an outside source:
- Soil moisture can migrate upwards through a damaged or non-existent vapor barrier.
- Water from faulty plumbing fixtures can remain within the floor, even after repairing the leaks.
- Improperly installed roofing systems may allow leaks that are not always detected right away.
- Moisture migrating through a concrete slab may evaporate as it nears the surface. The top of the slab may appear dry, but when covered, the water vapor continues to rise, damaging flooring and coatings.
Concrete Moisture Testing Methods
A variety of methods will detect and document concrete moisture characteristics. The best tests provide clear and accurate answers to moisture issues. The worst practices create more questions and add potential problems.
Let’s look at some of these practices and find out what works for your application.
- Plastic Sheeting: Nothing complicated here; just take a square of plastic and duct-tape it to the floor. There are no special techniques or standardized test procedures to follow. If you come back the next day and see moisture under the plastic, you know that at a specific temperature, the right relative humidity, a certain barometric pressure, and maybe the right level of sunlight or shade, moisture might collect under the plastic. Or maybe not. If condensed moisture is present, you still do not know how much moisture there is, where it’s coming from, whether it will persist at the same level over time, and whether or not it’s going to cause a problem with the particular material you want to place over it. If it’s dry under the plastic, is it ok, or is there still an issue that is concealed for now? In short, there are better methods available for not much more effort.
- Calcium Chloride Vapor Emission Test is an ASTM F1869 method that measures the amount of water vapor coming out of the concrete in a given period. An accurately weighed dish of anhydrous calcium chloride pellets is placed under a sealed plastic cover for 60 to 72 hours. The dish is then recovered and weighed again. The difference in weight due to moisture absorbed by the calcium chloride compound allows a calculated estimate of the pounds of moisture vapor emitted through the floor over a 1,000ft² area over 24 hours. This practical quantitative test is simple to perform and is a well-known and accepted industry standard. It provides much more information than the plastic sheet method, but it does have some limitations. Ambient environmental conditions influence the test, and it is not applicable for floors of gypsum concrete or with lightweight aggregates. Nor can it be used on floors treated with coatings or patching and leveling compounds.
- Concrete Moisture Meters provide rapid, non-destructive results and excel for taking multiple moisture readings over a large area. Contact pins or plates on the bottom of these hand-held meters read electrical impedance when held against concrete surfaces. An analog dial or digital display shows comparative moisture content for about the top 1in (25mm) of the slab. Moisture meters are an excellent way to create a moisture profile for a preliminary evaluation following ASTM F2659. Test results are a useful check before placement of floor coverings or as the beginning part of an overall survey. They are a snapshot of current surface moisture conditions but do not provide information about subsurface moisture, emissions, movement, or changes over time.
- Concrete Relative Humidity Probe Kits based on the ASTM F2170 test method are the most thorough and comprehensive tools used today for the analysis of moisture in the concrete. Moisture is usually higher toward the bottom of a concrete slab profile, with concentration reduced as the water vapor migrates upward. When the upper surface is sealed or blocked by floor coverings, the moisture will eventually equalize throughout the thickness. Because F2170 tests take readings below the surface, measurements are more accurate, with more predictable estimates of future moisture levels with flooring in place.
The procedure requires drilling 5/8 to 3/4in (16 to 19mm) diameter holes in the concrete slab and inserting hollow plastic sleeves. The sleeves serve as a guide for the insertion of electronic moisture/humidity sensors to a specific depth. Depending upon the manufacturer, sensor measurements are collected using a portable meter that connects to each sensor via a cable or wireless connection, then stored in memory for analysis and reporting. Calibration solutions to verify the performance of probes and meters assure test accuracy. Results provide a direct, quantitative measurement of relative humidity, and over time, a profile of moisture changes and migration through the slab. Testing at controlled depths mitigates the effects of variable surface moisture caused by temporary wetting or drying actions. Humidity levels can be monitored for an indefinite period if desired, and the holes are quickly repaired with common patching compounds when observations are complete.
We hope this blog post has helped you understand the methods and concrete moisture testing equipment used for concrete slab moisture testing. Please contact our testing experts to discuss your application today.
Testing Resources
Standard Test Methods, Specifications, and Practices
Individual test methods and specifications referenced in our product descriptions, blog articles, and videos are available for review or purchase from the professional organizations noted.
- ASTM International (American Society for Testing and Materials)
- AASHTO (American Association of State Highway and Transportation Officials)
- ACI (American Concrete Institute)
- State DOTs (Departments of Transportation)
- ISO (International Organization for Standardization)
- BS (British Standards)
- EN (European Standards)