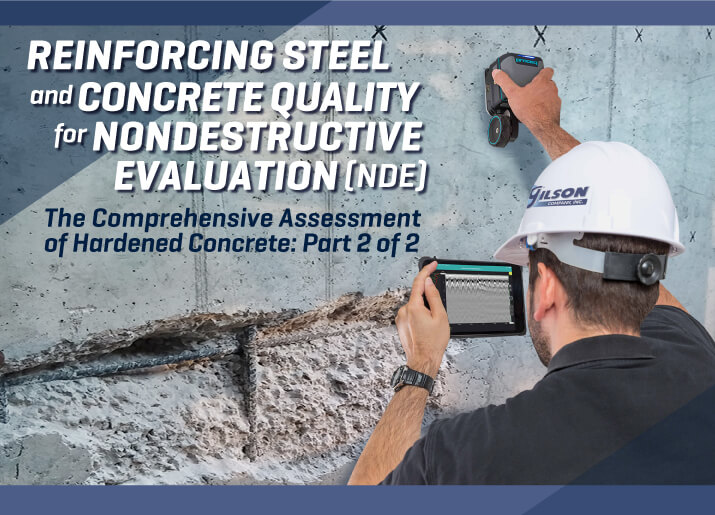
(This is Part 2 in a two-part blog series – Read Part 1 Nondestructive Testing of Concrete Compressive Strength.)
For the second of our two-part series on methods and equipment for the nondestructive evaluation (NDE) of hardened concrete, we are taking a close look at equipment to detect the location, orientation, and corrosion of reinforcing steel, the effects of moisture, and how to document the quality of the concrete itself.
Reinforcing Steel Detection, Location, and Size
Determination of the size, spacing, and three-dimensional location of reinforcing steel is vital to any analysis of a reinforced concrete structure. Documenting this information ensures compliance with the original design, aids in diagnosing current problems, and predicts future issues. If coring is required, it prevents damage to reinforcement and produces higher-quality samples.
Rebar locators and cover meters are available in a variety of models with different features and using different technologies. A suitable unit is selected based on the information needed and the degree of precision required.
- A simple metal detector can be helpful to avoid damage to steel bars from coring operations, but it lacks adequate precision to record exact location, size, and depth.
- Rebar locators and cover meters meet the requirements of British Standard, BS 1881, Part 204 Recommendations on the use of Electromagnetic Covermeters.
- Advanced (GPR) units provide complete profiles of concrete sections and even display three-dimensional modeling but may have more features than are needed for basic applications.
Electronic Metal Detector
The electronic metal detector scans concrete and other construction materials to detect embedded metallic objects. This economical device is simple to operate and detects metal at depths up to 6in (150mm). It works well for the preliminary scanning of large areas and the basic location of steel bars, electrical conduits, and tensioning cables. The detector can discriminate between ferrous and non-ferrous objects but lacks precision and features to document reinforcing steel size and depth accurately.
Rebar Locators and Cover Meters
Rebar locators feature simple operation but provide faster and more accurate bar locations, mid-points, and orientation than metal detectors. They provide enough precision for bar size and depth estimates, and advanced models offer data storage that can be uploaded to the user's PC. Most models provide visual and audible prompts for locating center points. Maximum detection depth is about 7in (180mm), and a #5 rebar can be accurately located to about 5.5in (140mm) deep.
Cover meters can locate reinforcing steel in concrete with accuracy equal to or better than rebar locators and offer better functionality to measure concrete cover and bar size precisely. Sufficient concrete cover over reinforcing bars is essential for adequate strength development of structural elements and reduction of corrosion potential. Cover meters offer options to optimize performance for deeper searches or for locating individual bars in areas of congested steel. Features are also available to allow convenient operation and superior data logging, graphing, and display.
Ground Penetrating Radar
Ground Penetrating Radar (GPR) scanning equipment goes beyond the detection and location of reinforcing steel and can offer a complete virtual image of subsurface conditions. GPR allows total assessment of a concrete section and depicts multiple layers and orientations of reinforcing steel, along with cracks, defects, and inclusions in the concrete matrix, location of conduits and ductwork, and overall dimensions.
Gilson GPR models feature advanced electronics to produce three-dimensional imagery with a clear presentation of subsurface data. GPR equipment is comparatively expensive and requires user training to operate and interpret results. Advanced assessments may require chipping or drilling of concrete cover to confirm results.
Detection and Mapping of Reinforcing Steel Corrosion
Reinforcing steel in concrete is normally passive to corrosion until chlorides from the environment penetrate the concrete matrix and initiate a flow of electrical currents. Active corrosion increases the volume of steel rebars, generating enormous pressures that crack and delaminate the concrete. Detecting existing corrosion in reinforcing bars and gauging the potential for future corrosion can prevent serious structural issues and extend the service life of structures. Monitoring corrosion is especially important in bridge decks, columns, retaining walls, and other exterior load-bearing elements.
Concrete Resistivity
Concrete resistivity meters are hand-held and portable for convenient use in laboratory or field applications. Sensors are arranged in a four-probe Wenner array to provide electrical resistivity values. These values have shown good correlations to concrete fluid permeability and susceptibility of the reinforcing steel to chloride-induced corrosion. Test methods are described in AASHTO T 358, and an ASTM method is pending. The resistivity meter is a fast, convenient alternative to the rapid chloride permeability test. It can be used to evaluate mix designs in the lab and to check reinforced concrete in the field to confirm similar properties and the potential for steel corrosion.
Corrosion Detection and Mapping
Corrosion meters detect and map the extent of corrosion activity in reinforcing steel systems. The half-cell potential method noted in ASTM C876 locates slight differences in the electrical potential of concrete surfaces that indicate the presence of, or potential for, steel corrosion. The meters use probes saturated with a copper/copper sulfate solution and require a direct connection to the reinforcing steel grid for operation. Readings can be marked on the concrete surface, or advanced models feature on-screen plotting or software to export to a PC for graphing.
Rapid Chloride Permeability
The rapid chloride permeability test is an older laboratory method noted in ASTM C1202 and AASHTO T 277 to determine chloride permeability characteristics of concrete mixes that lead to corrosion of reinforcing steel. Test cylinders or concrete core specimens are positioned between fluid-filled negative and positive electrodes, and electrical current flow is measured. The test is reliable but time-consuming to set up and perform and not easily performed in the field.
Concrete Condition
Cracking in concrete structures is not desirable, but it is not unusual nor is it always a significant problem. The onset and movement of cracking does warrant investigation, and there are test methods and equipment to measure and monitor cracks.
Cracking and Displacement
Cracking in concrete structures is not desirable, but neither is it unusual nor is it always a significant problem. The onset and movement of cracking does warrant investigation, and there are test methods and equipment to measure and monitor cracks.
- Crack width gauges and crack comparator cards are convenient for on-the-spot manual measurements of crack dimensions during initial surveys.
- Concrete crack data loggers document the movements of crack and joint openings at user-defined intervals and store the measurements in memory. A stainless steel cable spans the crack opening and is precisely measured as it winds or unwinds from its spool in the logger.
- Crack monitors are affixed to the concrete surface and designed to record the direction and amount of displacement over time. There are a variety of models and kits to fit different application requirements.
- Strain gauge sets offer very precise measurements of crack movements resulting from shrinkage, relative displacement, and strain under loading. The strain gauge set also meets the requirements of ASTM C490 for length change testing.
Moisture
Moisture in concrete can be an issue with significant effects on coatings and floor coverings, causing peeling, condensation, blistering, and delamination. Moisture may be constant, change over time, or migrate through concrete sections and be cyclical. Some home-grown detection methods, such as taping plastic over an area, may work to confirm a problem but do little to document or record the extent of the issue. There are methods and equipment to do the job right.
- Concrete moisture meters are used manually to measure the amount of water at the surface of a concrete element at a given moment. Readings of the electrical impedance between the probes indicates the degree of saturation. These meters are good for diagnosing moisture issues and defining wet vs dry areas when following methods in ASTM F2659.
- Moisture emission test kits meet the requirements of ASTM F1869 to determine the moisture emission rate through a concrete slab. The kit consists of a plastic dome placed and sealed over a calcium chloride container. The calcium chloride disc is weighed before and after the test period to calculate the weight of water emitted by the concrete within the test area.
- Humidity measurement kits use sensors embedded below the slab surface for periodic measurements of relative humidity in concrete. Humidity values are collected from the sensors by meters to provide a complete profile of moisture conditions throughout the slab, as required in ASTM F2170.
Pull-Off Testing
Pull-Off Testers measure the near-surface tensile strength of concrete and the bond strength of concrete repairs and overlays placed over the substrate. As described in the ASTM C1583 standard test method, a shallow core is cut into the test site, and a metal disc is affixed to the surface with an epoxy adhesive. The pull-off device draws the disc away from the surface and measures the tensile force until failure occurs.
When testing the concrete surface directly, the method is not widely considered a reliable indicator of compressive strength. Still, it establishes the surface's suitability to receive repair and overlay materials. The same device is also used to measure the bond strength of overlays and coatings to the original concrete. The test is easy to set up and can be performed on any concrete or overlay substrate with only minimal surface preparation.
Alkali-Silica Reactivity (ASR)
ASR detection is a simple test often used to confirm a destructive process already underway. A freshly broken concrete surface is exposed and sprayed with two chemical reagents for the test. A yellow stain after the first treatment indicates that ASR is present. A pink stain after the second treatment indicates the ASR is advanced.
ASR occurs when the presence of moisture aggravates a reaction between the highly alkaline cement paste and the silica compounds found in some reactive aggregates. The reaction causes a local increase in volume, and the expansive pressure cracks both aggregate and surrounding cement paste.
Aggregate reactivity in fresh concrete can be mitigated with lithium-based admixtures or electrochemical extractions, but the best prevention is early testing of aggregate sources for reactivity characteristics. ASTM C1293, C1260, and other tests for aggregates, or C1567 for combinations of aggregates and cementitious materials, are designed to screen aggregates before use.
Additional Resources
Related Gilson Videos
- Tracking Concrete Crack Movement
- Nondestructive Evaluation of concrete Using Ground Penetrating Radar
We hope this blog series has answered your questions on the evaluation of hardened concrete.. For more information on NDT instruments, visit our Non-Destructive Testing Equipment page. Please contact our testing experts for questions or help with your application.
Testing Resources
Standard Test Methods, Specifications, and Practices
Individual test methods and specifications referenced in our product descriptions, blog articles, and videos are available for review or purchase from the professional organizations noted.
- ASTM International (American Society for Testing and Materials)
- AASHTO (American Association of State Highway and Transportation Officials)
- ACI (American Concrete Institute)
- State DOTs (Departments of Transportation)
- ISO (International Organization for Standardization)
- BS (British Standards)
- EN (European Standards)