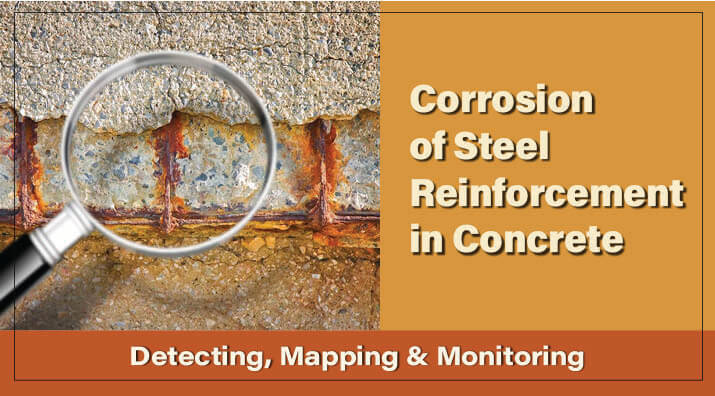
Data published by the National Association of Corrosion Engineers (NACE) over twenty years ago notes that the cost of damage caused by reinforcing steel corrosion in concrete highway bridges alone ran into several billion dollars at that time. Indirect losses for shutdowns, service disruptions, etc., dramatically increase the real total. All these expenses from damage to our nation’s infrastructure are borne by local, state, and federal agencies, or simply put, by you and me as taxpayers.
History of Corrosion in Concrete Reinforcing Steel
Corrosion of reinforcing steel has been recognized as a serious issue for well over a century. Two different reports in 1911, one regarding a meatpacking plant and another a marine jetty, found that electricity from lighting sources found a path through moist concrete and grounded out to embedded steel, causing rapid and severe damage to the concrete structures. By 1917, an extensive study of marine structures with no nearby electrical sources revealed that the deposition of water-borne chlorides and other salts in the concrete pores accelerated steel deterioration. Electrochemical corrosion mapping, the basis of modern methods described in ASTM C876, was first used in 1957 to study a causeway in California.
A network of bars, wire mesh, and tensioning cables crisscross reinforced concrete structures to increase strength. Embedded plates and anchors secure structural steel and various conduits route plumbing, electrical, and data utilities. Most of these embedded elements contain at least some metals prone to corrosion if not appropriately protected.
Causes of Corrosion in Concrete
We often think of steel-reinforced concrete structures in terms of strength, longevity, and permanence. However, like most metals, steel is an unstable material and begins to slowly return to its natural state of iron oxide, or rust, as soon as it is manufactured.
Just after concrete placement, a layer of passive alkaline material bonds to the surface of the embedded reinforcing steel in concrete, protecting it. Water with a high concentration of chloride ions from deicing salts or seawater forms an ideal electrolyte solution to promote electrochemical reactions. If this water migrates through cracks or the pore structure of the concrete, it will attack the protective layer on the steel.
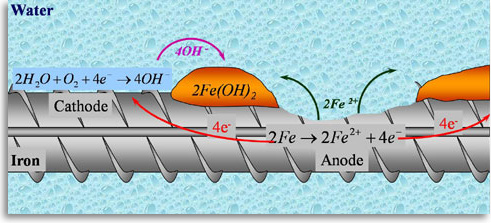
Corrosion begins when electrons migrate from electrically active points on the steel (anodes) to locations on the bar with the opposite polarity (cathodes). At the same time, ferrous ions lost from the steel diffuse into the surrounding concrete. When the electrolyte solution contacts an active area, iron hydroxide (rust) begins to form.
If the corrosion becomes established and is allowed to progress, it creates some big problems. Rust reduces the load-bearing capacity of the steel, lowering its effectiveness at carrying structural loads in tandem with the concrete. More concerning is that as the steel reverts to an iron oxide, its volume increases by two or three times, placing enormous internal forces against the surrounding concrete. The concrete loses its bond to the reinforcing steel, further reducing load capacity. Cracks form, allowing increased amounts of water, chlorides, and oxygen, accelerating the deterioration cycle.
The various strategies for delaying the onset and severity of corrosion focus on keeping the water/chloride mixture away from the reinforcing steel. Producing concrete mixtures that feature low permeability and reduced tendency for cracking, and providing adequate cover depth during placement are effective measures. Using corrosion inhibiting admixtures, coating of rebars, cathodic protection systems, and surface sealants are effective secondary measures.
Corrosion Prevention and Prediction
The best way to control concrete reinforcing steel corrosion is to make sure it never starts. Concrete mixes that have low permeability and resistance to cracking effectively restrict the ingress of water and chloride solutions.
Accurate estimations of the fluid permeability of hardened concrete and its chloride diffusion rate allow corrosion resistance to be evaluated either before or after the mix is placed on site.
There are two instruments that accurately estimate concrete permeability. Both measure the electrical resistivity of the hardened concrete matrix, a property proven to correlate well with concrete permeability to predict the likelihood of chloride ion penetration before it begins.
- Resipod Concrete Resistivity Meter is a portable handheld device that quickly measures surface electrical resistivity of hardened concrete. This versatile instrument is easily used on laboratory specimens to characterize mix design properties, on existing structures to estimate corrosion resistance, or on both, to verify that the concrete in place meets the mix design requirements.
The Resipod uses four electrodes fixed in a Wenner array to measure resistivity and conforms to AASHTO T 358 requirements. An optional accessory adapts the Resipod to measure bulk resistivity using the ASTM C1876 standard test method. This previous blog, Concrete Resistivity: A Guide for Nondestructive Testing, discusses the Resipod meter in detail.
- Rapid Chloride Permeability Tester performs bulk resistivity tests on concrete cores or prepared specimens in the laboratory. Current is measured between two ends of the specimen immersed in different solutions. The ASTM C1202 / AASHTO T 277 test method is limited to laboratory use and requires extensive sample preparation and testing time.
Corrosion Detection
Early detection of corrosion allows cost-effective strategies for mitigation. When damage is detected early and monitored, less expensive repair methods can be more effective. The most common procedures involve removing damaged materials in limited areas and replacement after cleaning and application of coatings for bonding and corrosion protection.
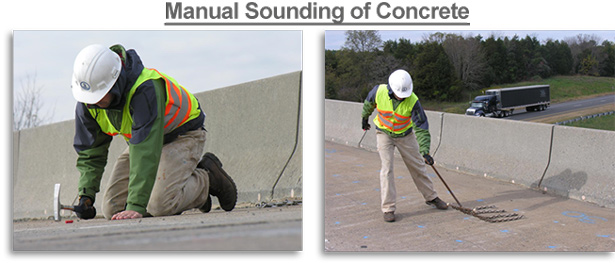
Sounding concrete surfaces is a low-tech way to assess and monitor general concrete quality and may detect the early stages of corrosion, subsidence of bases under slabs-on-grade, and large voids. The method is simple, tapping with a hammer or dragging a heavy chain across an area and listening for “dead” zones. Such areas should be marked for further examination with advanced nondestructive (NDT) test instruments.
Once a corrosion issue becomes severe, the problem becomes easier to spot visually. Obvious signs include rust stains on the surface, cracking, spalling, delamination over reinforcement, and exposed rebars. If the deterioration has reached this stage, options are sometimes limited to complete demolition and replacement.
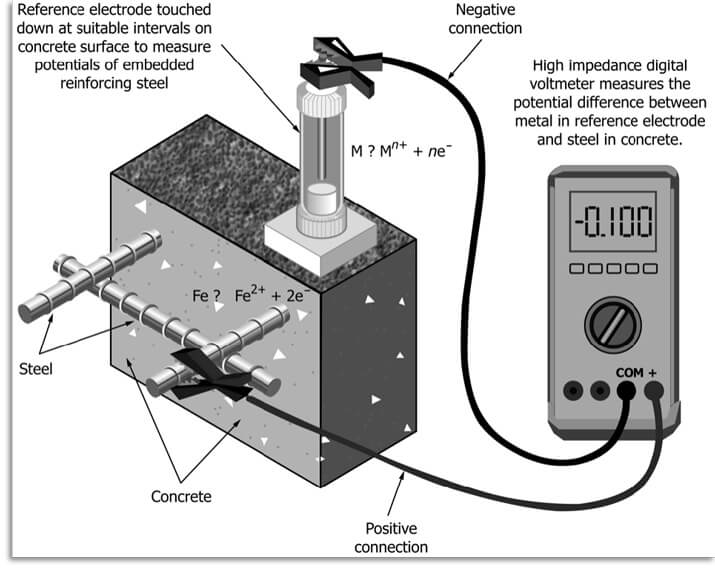
Corrosion Mapping and Monitoring
Mapping and continued monitoring of known areas of corrosion is the best way to manage the condition and limit the damage. The half-cell measurement method described in ASTM C876 is an accepted procedure to detect, quantify, and document the location and condition of corroded reinforcing bars in the concrete by measuring the electrical potential of the steel reinforcing network.
The system determines the current flow between a reference electrode and a connection made to the reinforcing grid. Connecting to the rebar requires locating a rebar and exposing a small section by chipping through the concrete. The entire rebar grid may not be electrically interconnected and could require testing for continuity.
The reference electrode consists of a copper tube immersed in a copper sulfate solution. The surface electrical connection to the concrete is made through a solution-saturated sponge at the end of the probe. After the grounding connection to the rebar grid is made, the operator simply pushes the saturated sponge against the concrete to acquire a reading.
The Concrete Corrosion Mapping System is an all-inclusive kit in a rugged transport case, ready to perform basic corrosion analysis using the copper-copper sulfate half-cell method on bridge decks, slabs, pavements, and reinforced concrete structures. The system conforms to ASTM C876. Readings are manually recorded on paper or marked with chalk on the concrete to document corrosion activity. A Rebar Locator is suggested for the accurate location of reinforcing bars.
We hope this blog post has helped you understand the corrosion of reinforcing steel in concrete and how to detect, assess, and manage it. For more information, visit our corrosion measurement equipment page, or please contact our testing experts for questions or help with your application.
Testing Resources
Standard Test Methods, Specifications, and Practices
Individual test methods and specifications referenced in our product descriptions, blog articles, and videos are available for review or purchase from the professional organizations noted.
- ASTM International (American Society for Testing and Materials)
- AASHTO (American Association of State Highway and Transportation Officials)
- ACI (American Concrete Institute)
- State DOTs (Departments of Transportation)
- ISO (International Organization for Standardization)
- BS (British Standards)
- EN (European Standards)