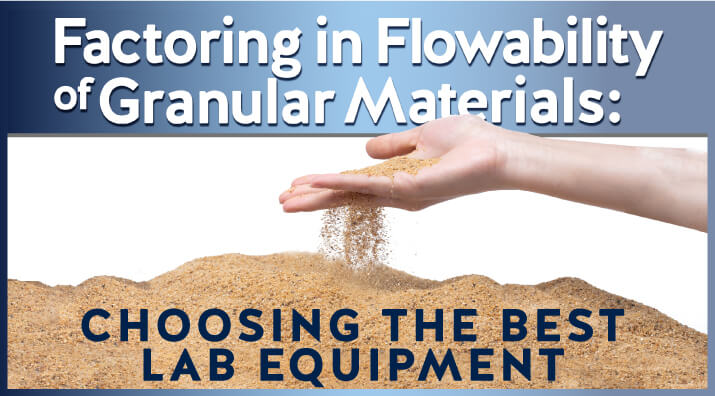
Product literature describing sampling and testing equipment for granular materials and powders often includes specific limits for particle sizes, volumes, or weight capacities. However, those values are not all-inclusive for every material under all conditions.
The materials under this umbrella have many characteristics that govern their movement and flow while being handled and tested. The selection of the most effective laboratory equipment for granular material is dictated by the nature and physical properties of the material and its condition during processing.
Flowability: How Does it Impact Sampling & Dividing?
Every stage of sampling, dividing, and testing granular material is affected by its flow properties. Understanding a particular material and the unique factors that impact its flowability increases the efficiency and accuracy of your laboratory testing and can even help control your budget. However, predicting the behavior of a material in advance can be challenging.
Fine-grained materials and powders with low specific gravities are known to form agglomerations under the influences of humidity, electrostatic attraction, and weak molecular bonds known as van der Waal forces. These forces are present in all granular materials but mainly cancel out with increasing mass and density.
With coarse and heavy granular materials, factors affecting flow are more often related to shape and surface texture. Particles classified as flat and elongated under a standard test method like ASTM D4791 can easily bridge splitter chutes or sieve mesh openings, hampering or obstructing flow. Angular surface textures cause particles to catch against one another and interfere with flowability.
The chart below shows some factors influencing the flowability of granular materials and powders and potential solutions to reduced flow.
Material Property | Improved Flow | Reduced Flow | Solutions for Low Flowability |
---|---|---|---|
Shape & Texture | Smooth, spherical particles flow easily over or around similar shapes | Flat and elongated particles or those with rough, angular textures snag other particles and restrict flow |
|
Relative Density (Specific Gravity) |
Dense materials respond more quickly to gravity, overcoming constraints and increasing flow rates | Low-density particles are more sensitive to the effects of moisture and static attraction and are less responsive to gravity, inhibiting flow |
|
Particle Size | Coarse particles resist cohesive and attractive forces, allowing them to move more independently | Fine particles and powders often form cohesive bonds, reducing flowability |
|
Moisture Content or Relative Humidity |
Surface moisture in coarse materials may lubricate particles and promote flow | Humidity or moisture causes fine materials to agglomerate, impeding flow and affecting particle size tests |
|
Electrostatic Attraction | Controlled humidity or electrical grounding may help control issues with static attraction | Fine, dry, lightweight particles may cling to sampling and testing equipment surfaces |
|
In this article, the emphasis is on particle sizing using test sieves and sieve shakers. We will guide you on selecting laboratory equipment matched to the qualities of your materials during sampling, dividing, and testing operations.
From Bulk Sample to Test Specimen: Finding Your Best Method
The splitting, or sample dividing, of bulk granular materials is a primary step toward producing a test specimen of usable size and weight. The accompanying chart shows a variety of devices and methods for sample dividing, along with their relative accuracy. The manual methods of cone & quartering, and scoop sampling are simple and inexpensive but introduce a high percentage of sampling errors.
Mechanical Splitters: Making Gravity and Flow Work for You
Mechanical chute splitters, sometimes called riffle splitters, consist of a row of angled chutes attached to a feed hopper. Material flows by gravity from the hopper through the chutes, discharging to each side of the splitter into two receiving pans positioned below. Single-stage riffle splitters divide bulk samples of granular material in half with each pass. Multi-stage splitters divide bulk samples into ½, ¼, or 1/8 fractions in a single pass, and they are fast and efficient when separating multiple testing-size specimens from large bulk samples.
Chute-type sample splitters are widely used because they feature simple and efficient operation with acceptable accuracy and are effective for a wide range of materials. Large samples of free-flowing material are efficiently reduced to test specimen size in a few passes, while repeated passes mix the sample material, preserving or enhancing sample homogeneity.
What do the Standard Test Methods Require?
Standard test methods often specify a minimum number of chute openings and chute width dimensions for riffle splitters. The ASTM C702 and AASHTO R 76 practices for reducing construction aggregate samples to testing size require no less than eight chutes for coarse aggregates or twelve for fine aggregates. These methods state that each chute must be at least 50% wider than the maximum particle size of the sample to promote even, continuous flow during sampling. However, materials containing undesirable flat and elongated particles may need chute openings two to three times the maximum particle size to avoid blockages and bridging in the chutes.
The published practices also require feeding the sample material evenly across the entire width of chute openings at a controlled rate. This technique takes practice to produce accurate results and can be highly variable between operators. Test method limitations may require several fixed-chute splitters to process materials with different properties. Even with multiple splitters, inconsistencies, and operator error could still result in test specimens that are not truly representative of the whole.
Gilson Recommendations: First, Match Your Splitter to Your Application
Gilson offers a diverse assortment of sample splitters designed for a variety of applications. Single or multi-stage models for a wide range of sizes handle sample-dividing demands in laboratory or production settings. Rugged fixed-chute devices are designed for particular test methods and materials, or models with adjustable chutes and gated hoppers offer versatility over a broad spectrum of materials. Enclosed splitters control hazardous dust and prevent sample loss.
Gilson Universal Splitters: Wide Range, Superior Accuracy
Universal Sample Splitters and Universal Mini-Splitters deliver the highest accuracy for the broadest range of material types of any riffle splitter in their class. The innovative features of this series are uniquely designed to enhance the optimum flow properties of any granular material.
Adjustable chute widths allow instant accommodations for diverse materials with different flow properties. If the chute width doesn’t work for your material, you can change it. The lever-release gated hoppers ensure uniform sample flow across the entire width of the chute with minimum operator input. Place the bulk sample in the hopper, distribute it evenly, and then pull the lever to let it flow uniformly across all the chute openings. A single Universal Splitter is meant to replace several fixed-chute models, meeting the demands of accurate representative sampling for various material types and sizes.
Riffle Splitters for Fine Materials & Powders
Gilson Precision Splitters allow accurate and cost-effective dividing of very fine granular materials and powders. These models are built with fixed-width chutes but retain the gated hopper design of the Universal series. Proportionally large hoppers, narrow gate openings, and the large surface area of the chute plates work together to encourage the efficient flow of fine particles through the system.
Increasing the angle of the chutes when dividing difficult materials is often the simplest solution to enhance flow. The Universal Mini-Splitters, the SP-2.5 Universal Splitter, and the SP-306 Precision Splitter feature chute angles of 60° instead of the conventional 45° angle to maximize flowability in fine materials.
Gilson Spinning Rifflers for High-Accuracy Sample Splitting
When the accuracy of representative sampling is critical, spinning rifflers, or rotary sample dividers, are acknowledged as the most reliable solution. These devices, described in a previous blog article, use a circular arrangement of sample receptacles positioned on a rotating turntable to capture precise fractions of material flowing from a vibrating feed trough. Flowability is central to the accuracy and efficiency of all rotary dividers, so accurate control of the hopper feed and vibration of the trough feeder is essential.
The spin riffling concept is scalable for a wide range of particle sizes and free-flowing granular materials.
- The Gilson Spinning Riffler divides 1L (61in³) samples of powders and fine-grained materials into as many as 16 glass vials ready for testing or sealing and storage with minimal handling.
- The Gilson Bulk Spinning Riffler handles large sample volumes up to 51L (1.8³) of granular material with particle sizes up to 2in (50.8mm). Representative samples are retained in four or eight stainless steel fraction collection pans positioned on the turntable.
Flow Tables: A Different Approach to Sample Splitting
A Sample Reducer, or inclined table, is a mechanical gravity splitter with a unique design for use in the labor field. Bulk sample from a hopper flows over an inclined surface past a series of prisms and openings that redirect and reject material. A specific fraction, often 1/16 of the bulk sample, is retained for testing. Sample Reducers are ideal for on-the-spot dividing of free-flowing products like proppant materials for hydraulic fracturing operations. Good material flowability is crucial for the effective operation of these devices, and the accuracy level is moderate for limited particle size ranges.
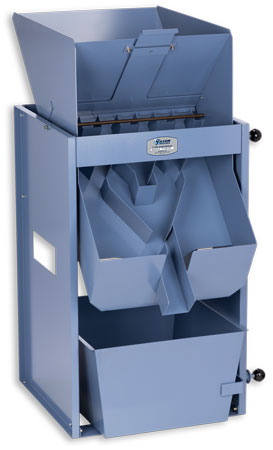
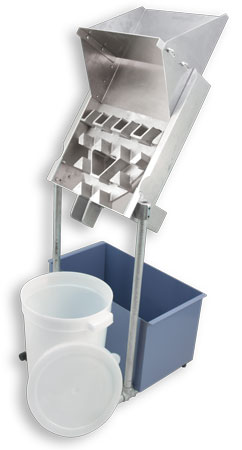
We hope this article has helped you understand the impact of flow characteristics on the performance of various sample splitter types and models. To discuss your specific application, please contact the Testing Experts at Gilson.