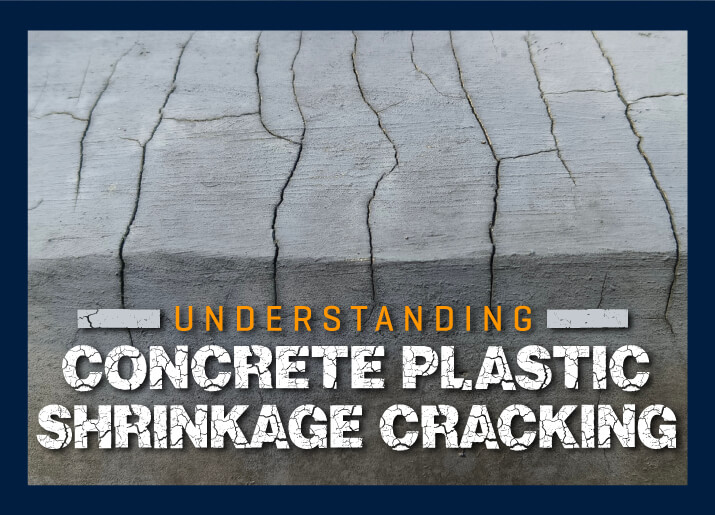
When you’re preparing for a pavement or slab-on-grade concrete pour and think you should smear on extra sunscreen or apply more lip balm before starting, you should also be concerned about plastic shrinkage cracking. Warm, breezy conditions, bright sunshine, and low humidity make for a lovely day, but those things are big red flags for the formation of shrinkage cracks on exposed pours. Ambient conditions are significant factors in shrinkage cracking, but concrete contents or mix design proportions can also be issues.
Plastic shrinkage cracking is often a problem on flatwork installations and tilt-up panels. Still, it can develop on the exposed top of formed walls or the horizontal surfaces of beams or foundations. When fresh concrete is placed, the heavier contents like aggregates and paste naturally migrate toward the bottom while the material is still plastic, forcing free water to the top. As this bleed water evaporates, the surface shrinks, along with the interior of the concrete. If the evaporation rate is too high, tensile stresses become greater at the surface but are restrained by the concrete below. Something has to give, so the stresses at the surface pull the concrete apart.
How Much of a Problem is Plastic Shrinkage?
Plastic shrinkage cracking appears during the first few hours after placement as long, often parallel, narrow cracks with a shallow V-profile. The cracks form before the concrete has developed significant tensile strength, and propagation stops once the concrete has achieved its final set.
If the migration of bleed water is slower than the evaporative rate, surface shrinkage creates tensile stresses, causing cracks to form.
Because the cracks are limited and primarily shallow, they are not often a significant threat to structural integrity. Still, they are unsightly cosmetic blemishes and undesirable on exposed architectural surfaces. If the cracks are widespread on exposed surfaces, water ingress through the cracks impacts the durability of the concrete, especially its resistance to freeze-thaw cycles.
Managing Plastic Shrinkage
Concrete formulations that resist plastic shrinkage are well within mix design capabilities but sometimes at cross-purposes with structural, architectural, and budgetary goals.
Modern concrete mixes designed for use in hot weather often use slow-setting cement types and set-retarding admixtures that contribute to plastic shrinkage cracking. Supplementary cementitious materials (SCMs) like silica fume, fly ash, and slag cement improve concrete strength and performance but increase water demand. Ice sometimes supplements mix water to slow down set times. These materials all retard bleed rates, causing evaporative losses from the surface to outpace the emergence of bleed water.
Other factors that aggravate plastic shrinkage crack development are prolonged set times and rushed finishing operations that remove bleed water, or worse, work it into the concrete, weakening the surface.
Assessing and Responding to Ambient Conditions
Adjusting the concrete mix design as a preventative measure to minimize plastic cracking is sometimes too difficult and expensive to be practical. Reactive methods that reduce surface exposure to sun, wind, and heat while increasing local humidity are more pragmatic and effective. Night-time pours can be an ideal solution in some circumstances.
A long-used rule of thumb for optimum concrete placement conditions goes something like this:
- Air temperature: less than 80°F (26.7°C)
- Relative Humidity: less than 50%
- Wind Speed: less than ten mph (16kph)
- Concrete Temperature: less than 85°F (29.4°C)
These values are not inaccurate, but on the other hand, they don’t occur all the time, nor is there guidance on what to do if conditions change on the day of your pour.
Fortunately, research by concrete engineers and technologists has provided some science-based strategies for managing plastic shrinkage problems. By paying attention to ambient conditions and knowing the characteristics of the concrete and admixtures being used, we can employ tools and countermeasures to mitigate problems.
The American Concrete Institute (ACI) technical committee 305 is responsible for developing and reporting hot weather concreting issues. Although combinations of temperature, humidity, and wind can cause high evaporation rates at any time of year, drying conditions are at their worst in hot, dry, windy weather. ACI publication PRC-305R-20: Guide to Hot Weather Concreting is free to ACI members, and even at full price, an invaluable resource for mixing and placing concrete in hot weather conditions. Some of the essential information in this publication involves determining how fast bleed water is evaporating from the concrete surface.
In 1954, Carl Menzel with the Portland Cement Association (PCA) submitted a paper that included a formula for calculating the evaporative rate of water:
W = 0.44(eo – ea)(0.253 + 0.096V)
Where:
W = weight (lb) of water evaporated per square foot of surface per hour (lb/ft2/hr),
eo = pressure of saturated vapor pressure at the temperature of the evaporating surface, psi,
ea = vapor pressure of air, psi, and
V = average horizontal air or wind speed in mph, measured at about 20in. above the evaporating surface.
The vapor pressure of air and the pressure of saturated vapor are values that are difficult to establish on-site.
In 1960, Delmar Bloem, an engineer in Iowa with the National Ready-Mixed Concrete Association (NRMCA) and National Sand and Gravel Association (NSGA), published a paper with an easier to use graphic representation based on Menzel’s equation. The widespread use of his nomograph continues today:
Evaporative rates less than about 0.2 lb/ft2/h (1.0 kg/m2/h) when placing traditional mix designs of this era would not cause undue concern. However, some of the advanced mixes in use today could be vulnerable at evaporative losses as low as 0.05 lb/ft2/h (0.25 kg/m2/h).
Preventing and Monitoring Plastic Shrinkage Cracks
The collection of data for evaporative rate determinations requires measuring devices suited to the task and properly positioned. Wind speed instruments should be positioned at the height of 20in (0.5m) above the surface to ensure calculations agree with the evaporative rate formulae. Measure the relative humidity and air temperature in a shaded area 4ft to 6ft (1.2m to 1.8m) above the concrete surface and out of the direct wind.
Ideally, monitoring of ambient conditions should start an hour before the concrete placement begins and continue at half-hour intervals until initial curing is complete. Reactions to the measured values could include shading areas from the sun, repositioning windbreaks, or regulating water-fogging devices.
Gilson's Equipment Recommendations
- Data Logging Thermometers are recommended for gathering and storing ongoing air temperature data. Gilson’s 4-Channel Data Logging Thermometer is rugged, accurate, and collects temperature from four wired probes simultaneously. A model with NIST certification is available.
- Relative humidity instruments range from old-style but reliable Sling Psychrometers to Temperature and Humidity Data Loggers with USB connections and live display.
- Environmental Meters are an all-in-one solution designed by concrete experts to meet ACI 305R requirements for monitoring conditions leading to concrete plastic shrinkage cracking. The pocket-sized units measure air temperature, wind speed, relative humidity, barometric pressure and calculate the evaporation rate, dew point, heat stress, and wind chill. Concrete temperatures are entered separately.
We hope this blog post on concrete plastic shrinkage cracking has helped you understand the issue and presented some strategies and tools for mitigating it. Please contact our testing experts for questions or help with your application.
Testing Resources
Standard Test Methods, Specifications, and Practices
Individual test methods and specifications referenced in our product descriptions, blog articles, and videos are available for review or purchase from the professional organizations noted.
- ASTM International (American Society for Testing and Materials)
- AASHTO (American Association of State Highway and Transportation Officials)
- ACI (American Concrete Institute)
- State DOTs (Departments of Transportation)
- ISO (International Organization for Standardization)
- BS (British Standards)
- EN (European Standards)