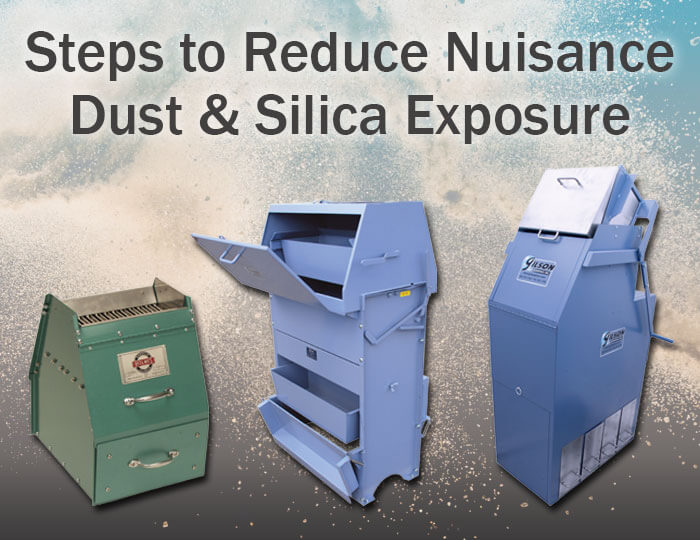
Exposure To Dust: What You Should Know
OSHA's Respirable Crystalline Silica standard for construction puts limits on the amount of respirable silica that workers may be exposed to. Among the construction-related industries affected by this standard expected to be impacted by the new rule are concrete products, ready-mix concrete, asphalt products manufacturing, and aggregates and gravel.
Crystalline silica is found in products commonly used in road and infrastructure construction – sand, concrete, stone, mortar, asphalt, cement, grout, brick, and tile. In addition, OSHA reports that silica dust can be generated in many construction activities, including cutting, sawing, grinding, crushing, sanding, and drilling.
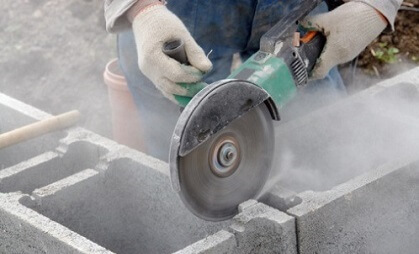
Photo Credit: https://www.cdc.gov/niosh/topics/silica/
This blog post will discuss protective measures that can be used in construction material testing in the laboratory or on the job site, to help reduce a worker’s exposure to silica and other harmful dust. It also provides information on respirable and/or nuisance dust that can typically manifest in non-construction industries.
How To Protect Yourself
Whether from the bulk splitting of aggregates, reducing pharmaceutical powder samples, or sampling dry bulk ingredients in food industry testing, fine powder emissions from splitting and dividing can cause nuisance dust in a materials testing lab. It’s important to know your equipment and if it is designed to control nuisance or harmful dust. Most equipment of this nature should be operated following at least a couple of basic guidelines:
- Operate only in properly-ventilated areas
- Wear protective masks or respiratory gear to prevent inhaling potentially-hazardous dust
- If the sample material has a Material Safety Data Sheet (MSDS), review it carefully for precautions
- Follow recommendations for Personal Protection devices and methods
It's Not Just Nuisance Dust
Nuisance dust can derive from sampling flour and other powders or granular materials as readily as it can from dividing aggregates. There are several factors to keep in mind about airborne particles that result from the sampling and dividing process:
- Silica is often in aggregates and minerals, iron ore, and even soil. As stated earlier, silica, also known as quartz, is common in materials used on construction sites, and construction industry processes such as cutting, crushing, and grinding can create not just nuisance dust, but “respirable silica dust”
- Coal and Coke are both by-products of mining and have long been associated with black lung resulting from "respirable coal mine dust"
- Flour and Grain can cause a condition known as "baker's asthma" which can arise from flour and grain dust exposure in the food industry, as well as in animal feed production.
- Biologically-Active Components found in drugs is a concern for worker's within the pharmaceutical industry, not only for possible health risks from dust inhalation but from breathing in biologically-active components of drugs.
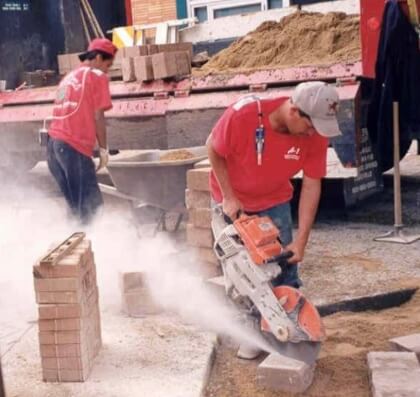
Photo Credit: Photo Credit: https://www.cdc.gov/niosh/topics/silica/
How To Reduce Dust and Protect Workers
Despite the issues raised above, nuisance and respirable dust can be significantly reduced by using equipment designed specifically to prevent particle release during a process. Consider implementing measures to limit or prevent dust exposure, protect workers, and ensure the workplace is compliant with OSHA, NIOSH, and other regulatory agency standards. Some easy steps to take include:
- Soak dry materials with water when working in the field to minimize dust blowing in the air
- Use Masonry Saws that distribute water when cutting or sawing
- Optimize ventilation to minimize dust
- Lab safety equipment such as masks, face shields, goggles, eye protection, and a respiratory device should be readily available and worn when mandated
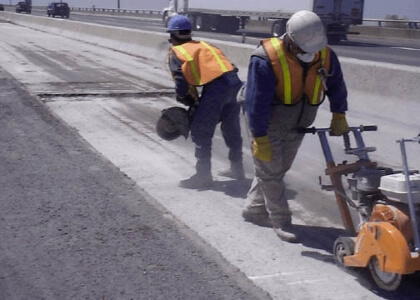
Photo Credit: Photo Credit: https://www.cdc.gov/niosh/topics/silica/
Preventing Nuisance Dust During Material Sampling
Sampling and dividing is a common procedure in testing materials used on construction materials and performed with a splitter or sample divider – a process that can emit a significant amount of dust.
There are numerous material sampling equipment types to choose from when working with materials known or believed to cause respirable issues, choose a splitter model designed to significantly reduce the amount of dust released into the air. In this case, an enclosed splitter is best for the job.
Enclosed sample splitters should be used when testing construction, mining, food, or pharmaceutical materials, the enclosed splitters we recommend help protect workers from dust.Selecting the type of enclosed splitter will depend on its use/applications, sample size, composition, and flowing capabilities. Gilson offers several types of enclosed splitters, each geared to specific applications, and designed to reduce dust.
- Gilson Totally-Enclosed Splitter performs well for construction field and laboratory testing and accommodates a wide range of large particles with accuracy and versatility.
- Gilson Quadri-Splitter works best with coal, coke, and mineral aggregates. Its moisture control capabilities perform as well in the dry desert climate of Arizona to retain moisture pr limit the uptake of hygroscopic moisture.
- Holmes Enclosed Sample Splitters are effective in dividing smaller samples of fine powders typically found in the food and pharmaceutical industries; their moisture control capabilities also make this splitter a good choice for dividing smaller coal and coke samples.
- Split-O-Matic Splitters, although not categorized as enclosed splitters the Laboratory and Production Split-O-Matics have features that can reduce the amount of dust generated.
- Dust enclosures or enclosure adapter sets are also available to modify standard Universal Sample Splitters. These optional sets retrofit existing splitters to reduce dust and eliminate sample loss.
Know the characteristics and composition of the items to be sampled. If powdery dust is emitted during the sampling process, understand that there could be health implications – and use MSDS or other published materials to explore what these implications are and how to prevent them in accordance with OSHA guidelines.
Finding Guideline Resources Online
The Internet has numerous sites with additional information and resources for reducing both nuisance and harmful dust, and protecting the workplace in accordance with federal, state, and local regulations. Check to see if your state has an agency dedicated to identifying and listing known hazardous aggregate minerals, including those with naturally-occurring elements that could pose health hazards from dust.
- The U.S. Dept. of Labor's Mine Safety and Health Administration (MSHA) website offers many resources.
- The Centers for Disease Control's National Institute for Occupational Safety and Health (NIOSH) has information relating to silica and workplace safety.
- Download Work Safely with Silica: Know the Hazard to understand the risks and how to mitigate them.
Testing Resources
Standard Test Methods, Specifications, and Practices
Individual test methods and specifications referenced in our product descriptions, blog articles, and videos are available for review or purchase from the professional organizations noted.
- ASTM International (American Society for Testing and Materials)
- AASHTO (American Association of State Highway and Transportation Officials)
- ACI (American Concrete Institute)
- State DOTs (Departments of Transportation)
- ISO (International Organization for Standardization)
- BS (British Standards)
- EN (European Standards)