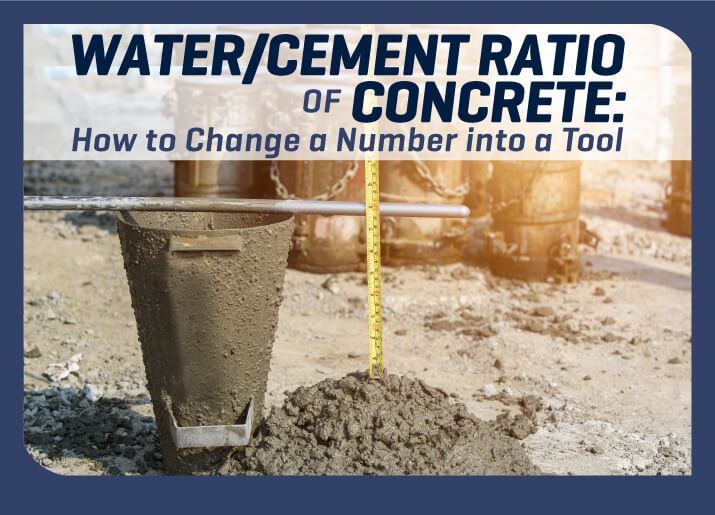
In 1918, Duff Abrams, a professor and research scientist at the Lewis Institute in Chicago (now the Illinois Institute of Technology), presented a paper that framed concrete as a composite material and showed that a mixture could be optimized for different applications through selection and control of the ingredients. His monograph would go on to influence the concrete industry for the next century and beyond.
The first and most significant element of Abrams' Design of Concrete Mixtures introduced a simple ratio comparing the weight of water to the weight of hydraulic cement (w/c) in a unit volume of concrete. The ratio was later redefined to include supplementary cementitious materials (SCMs) and is now expressed as w/cm. This ratio is recognized as a critical value, allowing the production of concrete with predictable and repeatable strength and consistency characteristics.
W/cm must usually be around 0.35 to fully hydrate all of the cement in a volume of concrete. However, a mix with a water content this low would have poor workability, meaning it will be challenging to place, consolidate, and finish. The completed structure or pavement would have a large number of voids and the potential for deficiencies in structural soundness, uniformity, and appearance.
For most mixes, the best w/cm ratio ranges from 0.40 to 0.60, depending on desired strength, consistency, or other characteristics of the concrete. A lower w/cm ratio reduces shrinkage and segregation while increasing strength, permeability, and durability. A higher ratio increases slump (workability) and reduces voids in the paste, but too much water leads to a reduction in strength and increased segregation.
So, there you are. We now have a simple value that lets concrete producers, contractors, testing labs, and engineers assess the future performance of every load of concrete before it even comes down the chute, right? Actually, no. W/cm is easy to calculate from mix design values but hard to measure quickly and accurately in a given batch.
Why is it So Hard to Determine the Real W/CM?
At the concrete plant, coarse and fine aggregates, cementitious materials, and water are individually weighed or proportioned for the selected mix design before being combined and mixed. Modern batching equipment nearly always ensures correct dispensing of the materials within specified tolerances. However, variables can enter the picture, especially after batching, that directly impact the w/cm ratio:
- The aggregates' moisture content and absorption characteristics must be known at the time of batching. If the aggregates are Saturated-Surface-Dry (SSD), a condition where each particle is fully saturated with water but dry on the surface, the total water content of the mix is not affected. However, free water beyond SSD results in a higher w/cm ratio, while drier aggregates absorb water and reduce w/cm. Testing to determine accurate aggregate moisture contents allows mix water corrections during production.
- After a previous load, wash water, and some concrete remnants often remain in a mixer truck's drum. If the amount of water is excessive, it can affect the w/cm ratio.
- For reasons both good and bad, water is frequently added to concrete before placement at the job site. Water added to the mix beyond that needed for hydration is sometimes referred to as "water of convenience," intended to improve workability and consistency. Someone may look at the concrete and arbitrarily decide that the load is too dry. A slump test may confirm that workability really is too low. Hot weather or an extended wait time before placement might cause a slump loss.
- Less often, there can be errors or equipment issues at the plant. Incorrect ingredient proportioning can occur due to programming mistakes, material sticking in bins or chutes, faulty batching equipment, or human error.
Whatever the reasons, changes to the w/cm ratio specified in the concrete mix design directly impact the slump, unit weight, compressive strength, and overall quality of the concrete.
What if Measuring Water/Cement Ratio was Easy?
A fast and accurate w/cm test would be a game changer. One of the most important properties of concrete could be a quality control tool instead of an approximate target value for batching. An effective test for w/cm ratio must quickly produce accurate results when performed on fresh concrete after mixing and before placement. If the actual proportions of water, cement, and aggregates are known at the moment of discharge, concrete quality is improved:
- Compliance with the approved mix design is verified, not assumed
- Proper batch plant operation is confirmed
- The strength and quality of hardened concrete is consistent and ensured
- Costs of removal and repair prompted by low strength tests are reduced
Over the years, approaches to measuring w/cm ratio have included methods based on electrical resistivity, turbidity, buoyancy/flotation, chemical titration, microwave heating, electron microscopy, backscatter from radioactive sources, and more. Some methods have been promising, but most have shortcomings in accuracy, test times, safety, or convenience that limit their effectiveness for quality control.
The AASHTO T 318 microwave heating method has had some acceptance based on its simplicity and ability to be performed on-site. Although the test is straightforward, it still has some drawbacks. A fresh concrete sample wrapped in fiberglass cloth is subjected to a series of drying intervals. Between each interval, the specimen is removed from the oven, weighed, broken up with a scraper, and returned to the oven for another cycle. After the initial interval, the process must be repeated every two minutes over 30 or 40 minutes until the interval decrease in mass is below 1g. In the end, the calculated results might vary ±0.05% from the actual w/cm values. The microwave oven used to perform the test is designed for food service applications, not the rugged conditions encountered daily in materials testing environments.
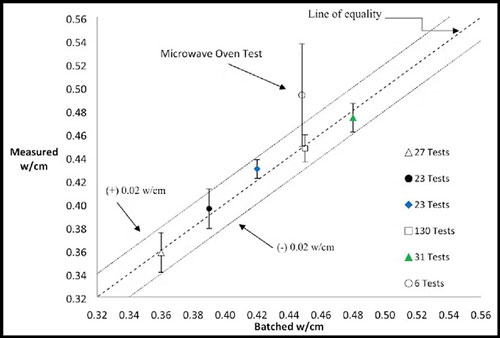
A summary of the measured w/cm with the Phoenix compared to the batched w/cm. One standard deviation is shown for each data point.
A New System Makes W/CM a Quality Control Tool
The Phoenix Water/Cement Furnace is an innovative new testing system that balances accuracy, simplicity, and speed to produce conclusive w/cm ratios accurate to ±0.01 in about 15 minutes. An AASHTO Provisional test method is currently under development for the Phoenix system. The equipment and test method work together to produce fast, accurate determinations of concrete water/cement ratio in laboratory or field environments.
The Concrete Phoenix System grew out of investigations by a team of researchers at Oklahoma State University. Multiple concrete mixtures using different combinations of aggregates, types of Portland cements, supplementary cementitious materials (SCMs), and admixtures were tested with the system, and results were compared with known w/cm values. The results of over 228 tests demonstrated ±0.01w/cm accuracy with a coefficient of variation of 3%. Research methods and findings are documented in a series of articles published in peer-reviewed journals.
When testing at the batch plant or job site, a delivered load of fresh concrete can be definitively accepted, corrected, or rejected in minutes, ensuring that only concrete of the specified mix design is put in place for the pavement or structure. In the lab, trial mixes can be verified quickly, adding a layer of quality control to the mix design process that is simple and effective.
The Phoenix Test Method
The Phoenix test begins with fresh concrete consolidated into a mold and weighed to determine the unit weight. The test specimen is transferred to a sample pan, weighed and heated in the furnace for about 15 minutes. While the Phoenix test cycle is running, other fresh concrete tests like slump, air content, and temperature can be performed, and test cylinders or beam specimens can be cast. On completion of the furnace cycle, the sample is weighed again to find the total weight of the lost water.
In the furnace chamber's super-heated environment, all the water is removed, including water trapped in the pores of aggregate particles. The batch ticket provides the weights of water, cement, aggregates, and admixtures, and aggregate specific gravity and absorption are known from previous lab tests. The measured unit weight of the fresh concrete is compared to the theoretical unit weight to correct for air content. Entering all the properties into the Phoenix app yields the precise w/cm in seconds.
The total elapsed time is about 20 minutes to measure the most essential property of a concrete mix. Not 28 days, not even an hour, this new quality control tool gives reliable and actionable answers while there is still time to fix a problem.
The Phoenix Furnace
The patent pending Phoenix W/C system is a true testing system. Similar test results cannot be duplicated using generic equipment because each component of the Phoenix system works together to generate accurate results:
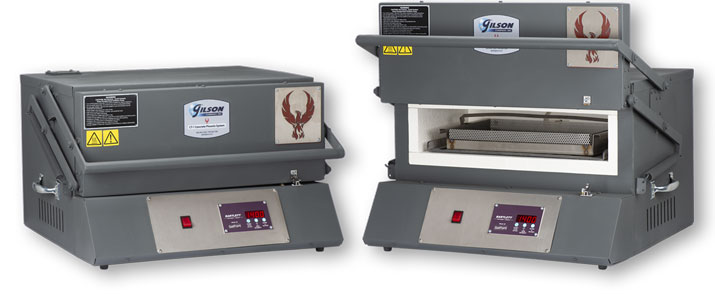
- The size of the mold is engineered to produce a reliable representative sample of fresh concrete that is easy to handle, and the sample pan is dimensioned to manage the surface area and thickness of the test specimen.
- Programming in the custom electronic controller regulates every step of the test cycle. Time and temperature are monitored closely to remove all moisture while ensuring minimal heat degradation to the aggregate.
- Dimensions and shape of the furnace chamber, size and positioning of heating elements, and the selection of refractory materials are engineered for precise, repeatable heating of the concrete sample with minimal thermal soaking time.
- An integrated exhaust fan removes hot gasses from the chamber and circulates air for maximum temperature uniformity.
- A smartphone preloaded with the Phoenix app is included with the test system. The app minimizes input and calculation errors, documents and organizes test results and notes, and streamlines the reporting process.
The Phoenix also provides rapid aggregate moisture tests at the batch plant in as little as 5 minutes.
Heavy galvanized and welded steel forms the outer case of the Phoenix furnace. The compact heating chamber is lined with rugged and dense ceramic-fiber firebrick, resistant to impact and abrasion. The heavy guillotine door lifts up and out of the way with one hand to eliminate contact with hot surfaces. Convenient lifting handles make transport and handling easy for remote locations.
A Safe Testing System
Testing equipment to evaluate construction materials must be equipped with reasonable safeguards to protect people and property. Even though users may already have some of the items required for the safe operation of the furnace, the Phoenix includes essential personal protective equipment and accessories to handle hot samples, maintaining the integrity of a dedicated testing system:
- Safety glasses, a face shield, and heat-resistant gloves protect the user from contact with hot surfaces and the radiant heat of the furnace.
- A cooling cage and loading fork distance the technician from the heat of the chamber and the hot sample.
- The firebrick weighing platform isolates the sample during weighing and protects the electronic balance. Hot samples can be weighed sooner for faster test times.
- A fire extinguisher and flame-retardant blanket stop the negative consequences of unintended contact with flammable items.
Independent Evaluations Prove the Value of the Phoenix System
The Minnesota DOT has evaluated the Phoenix method and equipment and is planning on implementation of the test by 2023. Oklahoma DOT is actively using their three Phoenix systems to gather data for review. Kansas, Utah, and New York DOTs have assisted in trial tests of the system and have shown interest in adopting it.
The PEM (Performance Engineered Mixtures) Pooled Fund Study with FHWA (Federal Highway Administration) and twenty state DOT partners are now evaluating the Phoenix method and equipment. The FHWA mobile concrete lab, used to showcase and demonstrate advancements in concrete testing methods, has installed a Phoenix Test System, and several key concrete producers and contractors are now utilizing Phoenix systems in their quality control programs.
We hope this article has helped you understand the Phoenix Water/Cement Furnace and testing system. Please contact the Testing Experts at Gilson to discuss your application.
Testing Resources
Standard Test Methods, Specifications, and Practices
Individual test methods and specifications referenced in our product descriptions, blog articles, and videos are available for review or purchase from the professional organizations noted.
- ASTM International (American Society for Testing and Materials)
- AASHTO (American Association of State Highway and Transportation Officials)
- ACI (American Concrete Institute)
- State DOTs (Departments of Transportation)
- ISO (International Organization for Standardization)
- BS (British Standards)
- EN (European Standards)