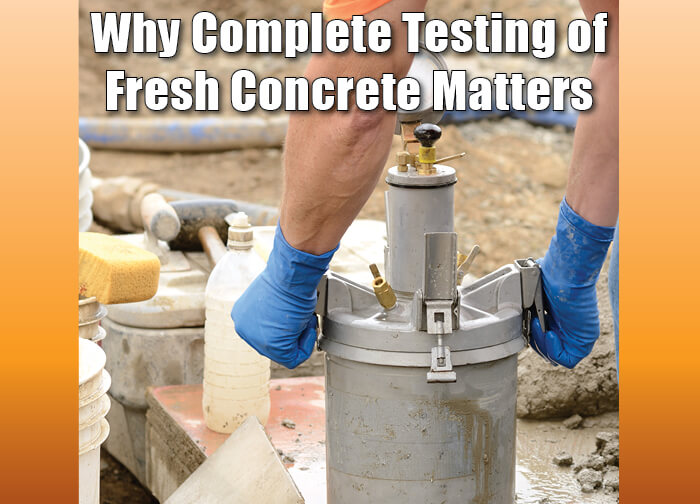
Why Does Fresh Concrete Testing Matter?
Not everyone sees a need to run all of the fresh concrete tests noted in ASTM C94 to determine compliance with the mix design. If values for air content or unit weight aren’t specified, why bother with those tests? My experiences proved otherwise.
The job was simple. Inspection and testing of one load for several interior columns on a hospital project where we were the testing lab. When I arrived, I set up just what was needed for slump and cylinders, hoping for a quick exit so I could cover some other projects on our schedule that day. I knew the mix design for interior columns called for higher compressive strength, but there was no entrained air requirement, so why test for it, right? Except that, as a chief technician for our small engineering company, I had just issued an edict that we would include tests for air content and unit weight for every set of cylinders we made, no matter the mix design or size of the pour. I knew that ultimately, running those tests was the last opportunity anyone would have to gather information characterizing the concrete delivered to the job.
I admit I was reluctant, but in my position, I had to walk the talk. And the walk is what I did; back to the truck to haul out the air meter and that heavy cast-iron crow’s foot scale. So by the time I had collected a sample and started my tests, one column was done and another started. I was going through the motions of the air test with the pressure meter trying to finish up faster, but the needle kept hanging up at about 6%. I was getting impatient, but I threw out the sample and started over. Again, 6% air content for a mix with none required. A little communication with the plant revealed this truck had been batched with a 4,000psi paving mix with 4% to 6% entrained air rather than the 7,000psi mix required for these structural columns. Not exactly a life-changing story, but they were able to dump the still-fresh concrete out of the 1 ½ columns and dispatch another truck within an hour or so. If I had run only a partial testing program on that load, there would have been big delays with jackhammers involved after the 28-day breaks came up short. The best part was the I-told-you-so lecture I gave my field technicians the next day.
As this story from Gilson VP of Operations Ben Backus suggests, there are a number of reasons why it’s important to test fresh concrete in the field, but one of the most important is to cover all your bases to assure you’re achieving quality control and assurance. Incomplete or improper testing can result in good concrete being rejected or bad concrete being accepted, so do the contractor, ready mix producer, owner, and yourself a favor by running the full battery of tests to gather information when it’s easiest to get.
What Are the Various Tests Performed on Fresh Concrete?
Fresh concrete tests measure factors such as strength, consistency, unit weight, air content, and temperature. By performing such tests consistently, you can detect changes in concrete that may affect its long-term performance. This post will focus on the importance of complete fresh concrete testing, including concrete air content, the role these tests play in guaranteeing adherence to QC/QA requirements, and some useful tips and equipment.
Why is it Important to Test Concrete?
Concrete naturally contains some air voids just from the batching process, typically 1% or 2%. Using an admixture to entrain additional air is a practice that ensures resistance to freeze-thaw cycles through the development of a system of air bubbles. These voids allow forces from the expansion and contraction of water and solids to dissipate without damaging the concrete.
Air Content:
The popular ASTM C 231 (AASHTO T152) pressure method for air content determination measures the change in volume of concrete with a change in pressure and is ideal for mixes with dense aggregates. Concrete Air Meters yield fast and accurate results using a method that is easy to run in the field. After proper placement of concrete in the bowl of the meter, air content is measured by pressurizing the upper chamber and releasing the volume of air into the lower chamber. The pressure gauge on the top of the meter indicates the change in sample volume as air pressurizes the bowl. An additional benefit of using a bowl with known capacity is the easy determination of unit weight by just weighing the same filled bowl (prior to the air test) on a field scale.
Necessary equipment includes:
- Type B Concrete Air Meter
- Compact Field Scale
- Pressure Meter Calibrator
- Tamping Rod
- Scoop
- Mallet
- Syringe
- Strike-off Plate
- Strike-off Bar
Tips
- DO: Clean and wet the internal surface of the bowl and cover before the test
- DO: Tap the sides of the air bowl sharply 10-15 times after rodding to close air voids left by the tamping rod. Voids can result in higher air content reading than the true value.
- DO: Tap the bowl’s sides with a mallet when pressurizing the bowl to help equalize the pressure.
Benefits
- An accurate and efficient way to determine the air content of freshly mixed concrete
- An easy way to also obtain unit weight information with a few added steps
- Equipment is highly accurate and easy to use
- A long-used and accepted method in the industry
Recommended Equipment
We recommend the Gilson Type B Concrete Air Meter with our exclusive Gorilla Gauge for superior accuracy and dual-layer safety glass to prevent breakage. This Concrete Pressure Meter also features:
- Long-lasting stainless steel clamps
- New Gorilla Gauge features tough Polyamide B unbreakable molded housing and ANSI-rated accuracy of ±0.5% of a full scale
- Brass petcocks with stainless steel ball valves for added accuracy and durability
- Sturdy plastic carrying case fitted to hold all necessary components for easy field transport
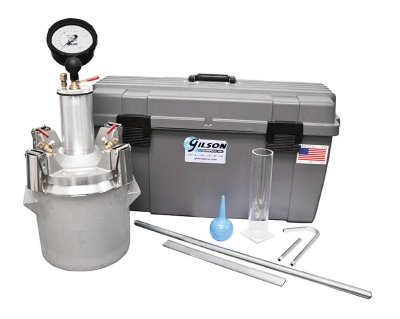
We also recommend Gilson’s Compact Field Scales
- Lightweight and portable with sturdy carrying case
- Electronic mechanism with digital display
- Accurate and repeatable weights
- Wide range of scale capacities from 13 to 440lb (6 to 200kg)
Visit our complete line of Fresh concrete testing equipment. For questions and more information speak to one of our experts at 800.444.1508.
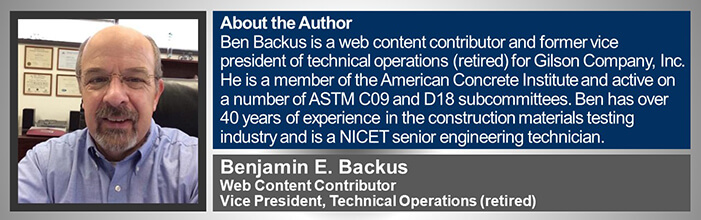