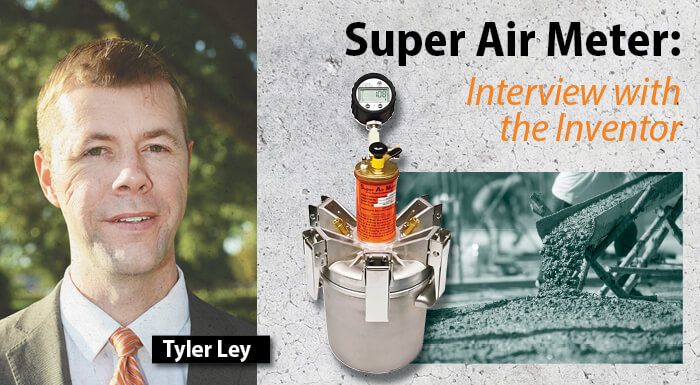
Tyler Ley, Ph.D., PE, is a Professor of Structural Engineering at Oklahoma State University, and by his own account, passionate about concrete. He is an ACI Fellow, active on a number of ACI committees, and is Chair of subcommittee 211-I, Assessing Aggregate Gradation. Dr. Ley was recently recognized by Concrete Construction magazine as one of 2019’s most influential people, and he has created a number of informative videos on concrete technology, which you can view on his YouTube channel. Dr. Ley invented and developed the Super Air Meter, a concrete testing instrument that promises to change the way we look at concrete’s freeze-thaw durability.
The Super Air Meter (SAM) looks a lot like a standard concrete air meter, and it does tell us the total air content of concrete, but it tells us a lot more besides. Using some special operational steps and a uniquely programmed digital pressure gauge, the SAM provides detailed insights into the matrix and structure of the air void system of a concrete mix. A test result from the Super Air Meter, called the SAM number, directly correlates to the size and spacing of air bubbles in the sample and is an accurate predictor of the concrete’s long-term freeze-thaw durability. The SAM is already in use in 39 states and 9 foreign countries and is being studied by a number of state and federal agencies. It has its own provisional AASHTO T 395 test method, and an ASTM test method is in development.
I’m grateful that Tyler could take some time recently to sit down with me and talk about concrete durability, the Super Air Meter’s role in adding value to our transportation infrastructure, and… um, beef tallow in cement! Read on.
Gilson: It seems like a lot of the concrete elements of our transportation infrastructure are showing signs of deterioration. What’s causing the damage to our concrete pavements and bridges?
Tyler Ley: I think a lot of things cause it, but one of the main things is that the concrete is deteriorating too early. Our concrete may not be the quality we want it to be while we are placing it. I think people do the best they can to make the best quality concrete they can, but it's a crazy process when you build five miles of pavement, and stuff slips in that maybe shouldn't. My big focus recently has been on developing test methods for fresh concrete to give important insights before it's hardened, so you know how it's going to perform when you're pumping it, vibrating it, finishing it, and how the freeze-thaw durability will play out. That's what the Super Air Meter is all about. I think that these new tools are really changing the game in our concrete infrastructure, but it's also going to take a little bit of changing the culture to get people to use them and changing thinking to not just wait until the concrete cures 28 days to evaluate it.
Gilson: So, the biggest impact we can have in improving concrete quality is to run useful tests right up front while it's fresh and while things can still be changed in the field?
TL: Yeah, you start with the mix design and when you're bringing all your materials together you need to make sure that they're producing a good durable mix. Then when you go to the field, make sure you're still getting that same mix, or at least those same qualities. These tests give us a lot more insight than what we had before. I think they're powerful and are going to be a big game-changer for our industry.
Gilson: When you say tests, are you talking about more than just the Super Air Meter? Are there other test methods the industry can use?
TL: The Super Air Meter for sure, but other fresh concrete tests as well. The box test is going to be an AASHTO standard this summer and gives you an idea of how concrete responds to vibration and its workability for slip-formed pavements, and the float test tells you about finish ability during placement. The Tarantula Curve is a systematic approach we’ve developed for optimizing aggregate proportions in concrete mix designs. So, why do we care about workability and finish ability? Well, if your concrete is really hard to place and finish and isn't constructible, you’re going to have to figure out a way to finish it. You may decide you have to add water or modify the mix just to get the concrete placed and finished. That’s not wrong, that’s your job. What’s wrong is that you’ve been supplied with a poorly designed mix that’s hard to handle.
Gilson: In other words, the contractor needs a quality mix supplied if they are going to deliver a quality product.
TL: Right! It’s really important to realize that they've got a job to do and we want to make it as easy as possible, so they don’t have to modify the concrete or expend extra effort or stress. If we can do this, everyone in the concrete world is going to benefit because of it.
Gilson: Concrete seems like pretty durable stuff. How can it be damaged by freezing temperatures?
TL: There's a 9% volume change when water goes from a liquid to a solid-state. If you have concrete that's in a wet environment and then freezes, it can definitely be damaged. Anyone who has left their favorite carbonated beverage in a freezer for too long knows what happens, right? If you want to try this, put a bag around it first 'cause it explodes all over the inside of your freezer!
Gilson: I’ve raised teenagers, so I know how that works!
TL: The reason that happens is that, again, the liquid turns into a solid and takes up a larger volume. When it happens inside the concrete, it happens on a very, very small scale. When those very small ice crystals start to form, they actually shove water through the pores and that water wants to find a boundary. And if it finds the outside of the concrete or finds an air entrainment void to move into, no big deal, the pressure is relieved. Those small air voids are the last to fill as the concrete becomes saturated, so they are extremely important. But if the concrete is completely saturated and there is no space left for the water to expand into as it freezes, it exerts tremendous pressures in tiny spaces and that’s when the damage starts. That's why we add air-entraining agents to concrete mixes to make all these small, well-distributed bubbles, so the water will have a place to go as it freezes.
Gilson: Ok, the air void matrix in concrete simply gives water a place to go as it freezes?
TL: That’s right, it’s like an escape hatch. The only thing I'd add would be that if those bubbles are too far apart, you're going to damage your concrete as pressure builds, but if the bubbles are close enough together, the water can easily reach a void, and everything will be great!
Gilson: How does an air-entraining admixture work to add bubbles to the mix?
TL: Air entraining agents are a soap or surfactant. When you add them to the wet concrete, they just create suds, like soap bubbles, that are dispersed through the mix and remain as intact bubbles in the hardened mix. I bet you didn’t know that the first air-entrained concrete mixes in the early part of the 20th century were accidental. One story about that is that some lubricant grease from machinery got into the cement powder during the manufacturing process, and another story is that a cement producer started adding beef tallow to the cement to make it easier to grind. People noticed that concrete from some suppliers was holding up really well, while other pavements were falling apart after a few freeze-thaw cycles. Researchers at the Portland Cement Association eventually figured out that these small air bubbles were being formed and began exploring how to make specific chemicals as additives that would make that happen on purpose. At first, air-entraining agents were part of the recipe for cement powder, and then a separate liquid admixture.
Gilson: The construction industry has always used a simple air content percentage range for acceptance of fresh concrete. Why isn’t that good enough now?
TL: What a great question! if you go back and look where the air entrainment specs that we currently use are from, they were developed in 1952 at the Portland Cement Association by Paul Kleiger and his team in a gargantuan research project to investigate why some pavements last and other pavements don't last. They actually kind of already knew that it was something to do with these accidental air bubbles, so his work focused on how to purposely make freeze-thaw durable concrete. His research showed that if the mortar fraction alone of the concrete had about 18% air by volume, it would result in a mix that met their standards for a freeze-thaw durable concrete. That value was later modified for industry use to an air volume of about 6% for the whole mix, depending on the amount of paste. This was groundbreaking work, but it was done with air-entraining agents we don’t use much anymore, and there are at least four other types used today. The concrete in the test batches didn’t have water reducers or supplementary cementitious materials, so no fly ash, no slag, no silica fume, nothing like that. The cements they used were totally different from today’s cements. Almost everything about our concrete today is different than it was in 1952. What technology do we still use today that was around in 1952? Not much besides our air-entraining specifications.
A lot of people have known for a while that total air volume is not as important as air void spacing. But the only methods we’ve had to measure spacing have been to cut the hardened concrete, polish it, and count the air bubbles under a microscope [ASTM C457], or to use the rapid freeze-thaw test [ASTM C666], which takes 3 ½ months, so it is not rapid at all.
Gilson: How does the Super Air Meter change this situation?
TL: One of the great things about the Super Air Meter is that it measures the air bubble spacing in the fresh concrete in about 10 minutes. The device gives you a number called a SAM number. The SAM number can be directly correlated to the hardened air void analysis and the freeze-thaw test. If you want a spacing factor of 0.008in, which a lot of people recommend for assured freeze-thaw durability, a SAM number of 0.20 confirms that measurement with over 85% accuracy. But even a SAM number of 0.30 indicates that you still have a mix with significant freeze-thaw durability with over 90% accuracy.
Gilson: What is the comparison in service life between a non-air entrained mix, a typical entrained air mix, and a mix known to have optimum size and spacing of voids?
TL: Let’s say this. If you're in a freeze-thaw environment and you have non-air entrained concrete, I think your service life – and I have this documented because people have accidentally made concrete pavements with no entrained air – your service life is 15 years or less. Air entrained concrete with an optimized air void matrix has a minuscule increase indirect costs, and yet you can expect as much as 40, possibly up to 80 years of performance, and those numbers are from modeling and freeze-thaw performance testing.
Gilson: What is the traditional method of characterizing the air void system in concrete?
TL: Traditionally, people would use the ASTM C457 method, which is also called a petrographic analysis of hardened air void analysis. You core or cut the concrete, then polish the flat surface and look at it underneath the microscope, count the air bubbles inside, and you get an air volume, something called the spacing factor and another term called the specific surface. You also get other values that are not as widely used. That's the traditional method.
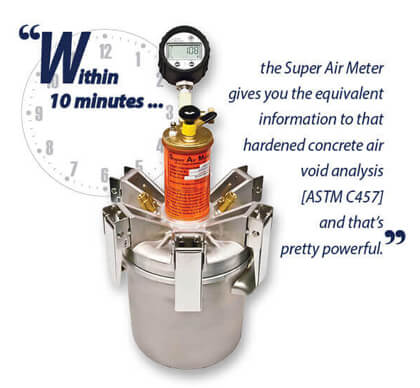
Gilson: Why shouldn’t we continue to use that?
TL: I think that method is great if you're dealing with hardened concrete and trying to figure out why it may not be performing the way you think it should, or if you just want to know all of the characteristics of the air void system. But it’s not a test that lends itself to rapid, on the spot evaluation of fresh concrete. Within 10 minutes, the Super Air Meter gives you the equivalent information to that hardened concrete air void analysis (ASTM C457) and that's pretty powerful. The Super Air Meter doesn’t replace that test, it just gives you the same type of information for fresh concrete so you can act on the test results. So I think it will help us make better concrete, to begin with.
Gilson: Describe the first thoughts you had that a typical air content test of fresh concrete could be modified to characterize air void spacing. Was it a light bulb moment?
TL: This is kind of like the genesis of where the Super Air Meter comes from. So, the amazing concrete technologist Ken Hover had this idea that you could get more information out of a standard concrete air meter. My Ph.D. advisor, Kevin Folliard, happened to be a summer intern for him when he was working hard on this concept. Every year in the multiple classes I took under Kevin, he would tell the story of Ken trying to get more information out of that air meter. It just totally intrigued me, so I started working on it during my Ph.D. We tried a bunch of stuff, but it didn’t really work. Then when I got to Oklahoma State University, I had a great master’s student named Braden Tabb working on a modified version of the air meter, using higher pressures than you would normally use in a standard Type B meter. I just happened to say to him one day, “Hey, if you've run a set of pressure steps on a sample, why don't you just run another set?” And we just ran three, or four, or five sets of pressure steps on the same sample. Theoretically, the results of the first set of pressure steps should be exactly the same as the second, third, fourth, and fifth. What he found was that the results were not the same between the first and second sets. He was running the tests on mixes from another project where we could manipulate air void quality. When the air void quality was bad, the number of differences between sets was very large. On mixes that we knew had good air void systems, the numbers were very small. Initially, we used five sets of pressure steps, but after a lot of comparisons with hardened air void analysis and field freeze-thaw performance testing, we reduced it to just three. I was so fortunate to have such a disciplined and focused student working hard and taking lots of careful measurements, and one day we just happened to measure something useful. So, it was more focus and diligence than a light bulb moment.
Gilson: Why should a testing lab consider buying a Super Air Meter? Is this a required field test?
TL: If you make or test air-entrained concrete and you want to have more understanding and more control over your air void system, then the Super Air Meter is a great test for you. All the new mix designs submitted in Colorado and Wisconsin must include Super Air Meter information and 12 different states are doing shadow testing with it, so lots of people are looking into it. The SAM is now used in 39 different states and nine foreign countries. The shadow testing means that these 12 states are collecting all the information for analysis and comparison to all the other testing data from their projects.
Gilson: The SAM looks pretty similar to a conventional Type B concrete air meter. Why does it cost more?
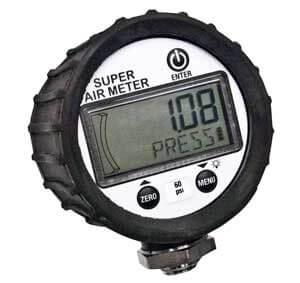
TL: Well, the Super Air Meter uses a digital gauge on top and that gauge is pretty important. That gauge does all the calculations that you need to do. It calculates air volume and something called the Super Air Meter number, and that number is what gives you an insight into the bubble spacing inside your fresh concrete. There’s other stuff too. The gauge tells the operator how to run the test, it watches the operator run the test and helps them avoid mistakes. If they do make a mistake, then it essentially just says “No, I'm sorry, you've made a big mistake and this is a voided test.” So, this Super Air Meter gauge does a lot more than a normal air meter and there are a lot tighter tolerances on it and a lot more things that are checked in the manufacturing process.
Gilson: Should testing labs equip every field technician with a Super Air Meter?
TL: That is an interesting question. That is going to depend on what stakeholders in the process want you to do. I wouldn't start out doing that, but I would use the Super Air Meter every single time I do a trial batch with air-entrained concrete because I think it tells you a lot. Then, when I went to the job site for the first time, I would run SAM tests to see how the field data compares to my lab data because there are opportunities for things to be different in the field. There are lots of things that could change, and you want to benchmark it to see where it's at. Now you have those numbers early on in the production of the concrete, and if you start to have problems in the field, you can bring the Super Air Meter back out and instantly compare your new information to your previous benchmark data. I would continue to take a SAM measurement every week or two, or whatever makes sense in the production schedule, just to see where you’re at. So, I don't think necessarily every single technician needs one of these for now, but I do think since we're just introducing this new concept people should try it to see what they can learn from it. I also think going into the future, more and more people will want to use these meters regularly.
Gilson: So, a testing lab might have one or two technicians trained on using the SAM that just circulate to use it on different projects as needed?
TL: Right. That’s a good approach.
Gilson: How is the test performed? Is extensive training required?
TL: Let's answer the second question first. No, I don't think extensive training is required. But I do think that it's not your normal air meter, and I think you need to know the people you outfit with it are trustworthy and that they're going to do a good job. When we've seen these people get their hands on it, they don’t take long to learn how to use it. Some of them watch YouTube videos and just do it. Other folks may have developed bad habits when running a normal Type B meter and they just need some modification to their habits to run the SAM test properly. You just need diligent people that pay attention. Extensive training isn’t needed.
A test with the SAM meter is performed exactly the same as with any standard Type B air meter, except that you use two sequences of three pressure steps. The best way to understand the details of this pressurization process is to just watch this YouTube video.
Gilson: Why are the three pressure steps applied in two sequences to the same specimen?
TL: When you do those first three pressure steps, what you're doing is applying pressure to the air void system. If the bubbles are farther apart, as you increase the pressure the smallest air bubbles get smaller and smaller and then they dissolve. With the second sequence, those bubbles aren’t there anymore and so you end up with a large difference in the response between the first and second pressure applications. On the other hand, when the air void matrix of a concrete mix is good and the bubbles are close together, they’ll get smaller as the pressure increases, but they won’t dissolve. That means when you decrease the pressure and apply it for the second time, most of the bubbles are still there. Then the SAM number, the difference between the two 45psi pressure steps, will be much smaller. We did a lot of comparisons between hardened air void analysis results and SAM numbers and freeze-thaw testing and SAM numbers and that's how we came up with the limits. The outside limit for freeze-thaw durability with a SAM number is 0.30, which is what we call the cliff of doom. After adjusting for a safety factor, the limit most specifications recommend is 0.20.
Gilson: Are experience and training required to interpret the test results?
TL: I don’t think so. The air content can be interpreted in the same way it always has and the SAM number doesn’t require much interpretation as an acceptable value. If the SAM number is less than 0.30, I would expect freeze-thaw durability. Historically, most people have said that a spacing factor of 0.008in, determined in the ASTM C457 tests, should be the number that determines acceptable freeze-thaw durability. To align with a spacing factor of 0.008in, the SAM number needs to be at 0.20.
Gilson: That makes sense. A technician or anyone looking at a report doesn’t need to plug the SAM number into an equation for analysis. It’s either thumbs-up or thumbs-down for acceptance.
You said earlier that the SAM test is rapidly becoming more popular and a lot of transportation agencies are either requiring or examining it. I see AASHTO now has T 395 as a provisional standard. Do you anticipate an ASTM method soon?
TL: We are working hard with ASTM to come up with an ASTM version of the AASHTO test method. That process is taking some time, but we’re making good progress and I hope to see an ASTM standard soon.
We hope this interview has helped you understand the Super Air Meter and its applications a little better. Visit Gilson’s website for more information on the Super Air Meter, or contact us to discuss your application.
Testing Resources
Standard Test Methods, Specifications, and Practices
Individual test methods and specifications referenced in our product descriptions, blog articles, and videos are available for review or purchase from the professional organizations noted.
- ASTM International (American Society for Testing and Materials)
- AASHTO (American Association of State Highway and Transportation Officials)
- ACI (American Concrete Institute)
- State DOTs (Departments of Transportation)
- ISO (International Organization for Standardization)
- BS (British Standards)
- EN (European Standards)