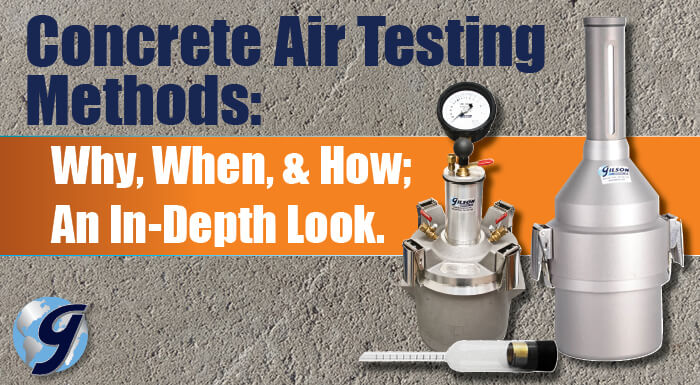
Air Content in Concrete Mix Design
The primary purpose of entraining air in concrete is to increase its durability when exposed to freeze/thaw cycles with water present. Air-entraining admixtures for concrete create small, uniform, and stable air bubbles from around 0.01mm to 1mm diameter in the cement matrix throughout a concrete mix. The bubbles become air voids in the hardened concrete, creating a relief system that allows the expansion of water as it freezes without damaging the concrete.
Additional benefits include:
- A decrease in water demand for mixing and curing
- An increase in workability
- A reduction in bleeding and segregation
Air Content Testing: Why is it Important?
Even for concrete mixes that do not require air-entraining admixtures, air content testing is still recommended to profile characteristics of the batch. Most non-air-entrained concrete contains between 1% and 2% entrapped air, and some admixtures may unintentionally entrain even more air.
ACI 301-16 Specifications for Structural Concrete and ACI 302.1R-15 Guide to Concrete Floor and Slab Construction indicate that air contents higher than 3% may require extra effort when finishing some mixes, leading to surface defects and delamination. Air content tests on non-air-entrained fresh concrete can prevent issues before they occur or be a valuable troubleshooting tool. One of Gilson’s previous blog posts Why Complete Testing of Fresh Concrete Matters discusses the importance of complete testing of fresh concrete.
Air Content Testing: When and Where
Just as putting air-entraining admixtures into concrete creates beneficial air bubbles, mixing, transporting, pumping, and handling the mix can take them out. So, not only is air content testing essential but so is testing at the right time and place. If the testing agency were only confirming the properties of the concrete as delivered to the job site, an argument could be made for testing only concrete sampled directly from the delivery truck. In truth, most stakeholders in a project are better served with more complete information, and it is often specified that the concrete be sampled at the point of placement, such as at the discharge end of a concrete pump. This can create difficulties in accurately sampling and testing fresh concrete and requires planning by the testing agency and cooperation with other trades.
This blog post examines the differences between the three recognized types of air content test methods and helps you select testing equipment best suited for each method.
1. Pressure Methods for Air Content
Type A and Type B concrete air meters use different techniques to apply air pressure to a concrete specimen that compresses the air voids in the sample. Differences in volume before and after compression indicate apparent air content, which is corrected to exclude air voids in aggregate particles. The pressure method cannot be used on mixes containing lightweight aggregates, blast furnace slag, or other aggregates with high porosity. Detailed test procedures for both types of meters are detailed in ASTM C231 and AASHTO T 152. Both meters use similar methods to consolidate fresh concrete into the measuring bowl, or pot. Concrete is deposited in three equal layers, and each layer is rodded 25 times with a tamping rod. The concrete is leveled off with a strike-off bar or plate, so the volume in a given bowl is the same each time.
Type A concrete air meters are fitted with a sealed graduated cylinder in the cover. After the sample is consolidated, the cover is clamped into place and filled with water. A specified pressure is applied to the assembly using an external pump or squeeze bulb, compressing the air voids in the specimen and lowering the water level. After releasing the pressure, the water level in the cylinder rises. The difference between the two levels is read from the cylinder graduations to determine the air content.
Pros
- Reliable results
- Tests normal weight concrete mixes
- Air Meter Calibrators provide a convenient field check of accuracy
Cons
- Testing requires more time and water than Type B meters
- Graduations in the sight glass are more challenging to interpolate than Type B gauge markings
- Cannot be used for concrete mixes using lightweight or porous aggregates
- Calibration is affected by changes in barometric pressure
- Requires determination of an aggregate correction factor
Best for
- Most concrete mixes using normal-weight aggregates
Type B concrete air meters incorporate an air chamber in the cover that is pressurized with an integral pump to a predetermined initial pressure once the cover is placed on the pot. A small amount of water is added to the assembled unit to displace free air, and the petcocks are closed. The pressurized air is released into the lower chamber and compresses the concrete specimen. The calibrated gauge displays the pressure difference directly as the total percent air content.
Gilson’s exclusive HM-30D Type B Air Meter features a rugged digital pressure gauge with rated air content accuracy of ±0.25%. Testing procedures are essentially the same as conventional Type B meters fitted with analog dial gauges. Test results are more accurate and consistent, and calibration and accuracy checks are faster and easier to perform. The polycarbonate and ABS plastic backlit gauge displays large, easy to read characters and is housed in an IP67 weatherproof enclosure. The Digital Gauge is available as an easy-to-install replacement for old-style dial gauges with 1/4in NPT connections.
Pros
- Fast, reliable results
- The test method is easy to perform and requires little training
- The most widely used method has proven performance
- Test results are unaffected by changes in barometric pressure
- Air Meter Calibrators provide a convenient field check of accuracy
Cons
- Cannot be used for concrete mixes using lightweight or porous aggregates
- Requires determination of an aggregate correction factor
Best for
- Most concrete mixes using normal-density, low-porosity aggregates
- Easy and efficient testing for any size project
Super Air Meter (SAM) is a modified Type B concrete air meter invented by Tyler Ley, Ph.D., PE, who promises the SAM will change the way we view concrete’s freeze-thaw durability. (To read more about Tyler, see our Tyler Ley Interview blog post with Dr. Ley himself).
The SAM uses an extended test procedure to determine air content and characterize the size and distribution of air bubbles in the concrete mix. The SAM and test method are important steps forward to increase freeze/thaw durability prediction in exposed concrete. It is used in several U.S. states and foreign countries.
The first part of the SAM test procedure meets all the requirements of ASTM C231, and the SAM can be used in place of the standard Type B meter for this application. After completion of the air content test, additional increments of pressure are applied in two sequences. Pressure differences are recorded and used to correlate average air void spacing. The complete SAM method is detailed in AASHTO T 395, and an ASTM method is pending.
Pros
- Characterizes air content and air void size and distribution for freeze/thaw durability performance predictions
- Test results in 10 minutes versus weeks or months for other air void evaluations, such as ASTM C457
- Determines standard C231 air content in the same testing sequence
Cons
- Equipment cost is higher
- Cannot be used for concrete mixes using lightweight or porous aggregates
- Requires determination of an aggregate correction factor
Best for
- Exposed concrete in cold-weather climates
- Infrastructure projects requiring freeze/thaw performance predictions
2. Volumetric Methods
Volumetric air content tests start with a concrete specimen of known volume consolidated into a container. A cover with integral graduated markings is sealed on the top and filled to a zero point with either water, isopropyl alcohol, or both. The entire assembly is then agitated vigorously, and the air voids are effectively washed out of the specimen. The difference in fluid levels before and after agitation is recorded as the air content.
Roller meters are usually constructed of aluminum (Roll-A-Meter), plastic (Volumetair Air Meter), or brass with a measuring bowl of at least 0.075ft³ (2.0L). The top section clamps to the bowl and includes a transparent graduated scale. Concrete is consolidated into the bowl, and the top section is clamped in place. The assembly is then filled with combinations of water and measured amounts of isopropyl alcohol, as detailed in ASTM C173 and AASHTO T 196. Some concrete mixes produce large amounts of foam after agitation, and the alcohol disperses the foam to allow more accurate fluid level readings.
Pros
- The method can be used for all concrete mixes, regardless of aggregate type
- Calibration of the apparatus is easier and required less frequently
- No need for an aggregate correction factor
Cons
- The test is time-consuming, requiring repeated cycles of agitation and resting until readings stabilize
- The agitation method is physically demanding
- Scale graduations are less precise than Type B gauge
- Some concrete mixes may require 1.4L or more of isopropyl alcohol per test
Best for
- Concrete mixes using lightweight, porous, or slag aggregates
- Less expensive plastic meters are best suited for occasional use
Chace Air Indicator Kit is a bit like a miniature roller meter, but the size of the specimen limits them to testing just the mortar portion of concrete mixes. There is currently no published standard for the kits. However, they are still useful for gauging the uniformity of fresh concrete during a pour when correlated to a conventional concrete air meter.
A brass cup mounted on a rubber stopper is filled with mortar. A glass vial with a graduated neck is pushed onto the stopper and filled to zero with isopropyl alcohol. The assembly is then agitated, and the difference in fluid level noted before and after agitation is observed for correlation with standard air meters.
Pros
- Pocket-sized portability
- Fast and easy checks for uniformity
- Good companions to conventional concrete air meters
Cons
- Test results are not precise
- Chace test results should not be the basis for acceptance or rejection
Best for
- Correlating with a calibrated pressure meter or roller meter for field estimates
- Quick, on-the-spot estimates to check the uniformity of batches during a pour
3. Gravimetric Method
The gravimetric method for calculating air content is part of a procedure in ASTM C138. AASHTO T 121 also determines the unit weights and yield of a concrete batch. Equipment for performing this test includes unit weight measures, strike-off plates, tamping rods, and field weighing scales. Fresh concrete consolidates into a unit weight measure, then carefully struck off and weighed. From there, a series of calculations are performed using the specimen weight and actual batch weights of the mix to determine the unit weight, density, yield, air content, cement content, and other properties of the mix.
Pros
- Results provide information and data for a wide range of concrete properties using just one procedure
Cons
- The test procedure and calculations can be time-consuming
- An accurate result requires complete knowledge of exact batch quantities
- Slight variations in test procedures, mix proportions, or specific gravities cause relatively larger errors
Best for
- Testing of trial mix designs
- Providing data for comparison to other tests
We hope this discussion of methods and equipment for air content testing of fresh mixed concrete has been helpful to you. Please contact us if you have any questions about your application.
Testing Resources
Standard Test Methods, Specifications, and Practices
Individual test methods and specifications referenced in our product descriptions, blog articles, and videos are available for review or purchase from the professional organizations noted.
- ASTM International (American Society for Testing and Materials)
- AASHTO (American Association of State Highway and Transportation Officials)
- ACI (American Concrete Institute)
- State DOTs (Departments of Transportation)
- ISO (International Organization for Standardization)
- BS (British Standards)
- EN (European Standards)