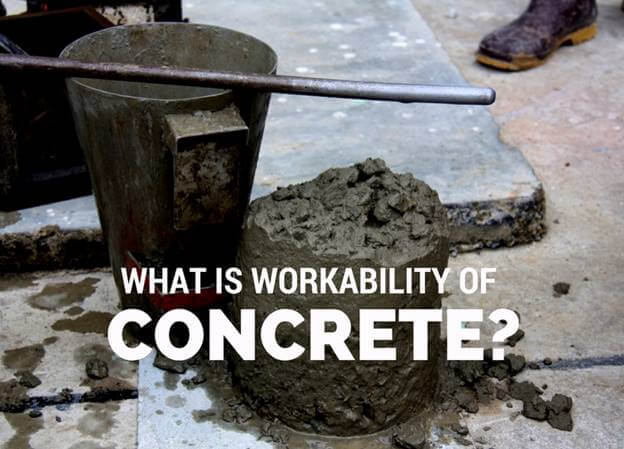
Table of Contents:
- Introduction to Workability
- Factors Affecting Workability
- The Slump Cone
- Types of Slump
- K-Slump Tester
- Self-Consolidating Concrete
What is the Workability of Concrete?
Workability of Concrete is a broad and subjective term describing how easily freshly mixed concrete can be mixed, placed, consolidated, and finished with minimal loss of homogeneity. Workability is a property that directly impacts strength, quality, appearance, and even the cost of labor for placement and finishing operations. But opinions don’t matter much when testing and documenting concrete properties, so how are these qualitative characteristics defined in quantitative terms? This blog post will cover everything you need to know about concrete workability, factors that can affect it, tests that define it, and slump testing equipment to test it.
Good Workability Means Different Things to Different People
There are different expectations and agendas across the design/construction team spectrum when it comes to optimum concrete design.
- The structural engineer wants higher strength and a good bond with reinforcing steel.
- The architect is concerned about cosmetic appeal.
- Bearing capacity is attractive to the owner because it allows smaller cross-sections of structural elements like walls and columns and, therefore, more usable floor space.
- A laborer needs a mix that can be moved, placed, and consolidated efficiently.
- A finisher is looking for something that takes a durable, high-quality finish quickly and easily.
A concrete mix with good workability brings many attributes together in balance and results in a quality product with long service life.
Factors Affecting Workability
Proportions and characteristics of materials and properties of admixtures all have an impact on the workability and other qualities of every concrete mix design; factors affecting workability include:
- Water/Cement Ratio: a higher proportion of cement or cementitious materials usually means greater strength, and with the proper amount of water, more paste coats the surface of aggregates for easier consolidation and a better finish. Not enough water for proper hydration means poor strength development and an uncooperative mix that resists easy placement and finishing. Adding excessive water could be said to increase workability because it makes it easier to place and consolidate. However, the negative impact on segregation, finishing operations, and final strength can be so detrimental that it should be approached very cautiously. Water to a cementitious material ratio (w/cm) of 0.45 to 0.6 is often the sweet spot for the production of workable concrete.
- Aggregate Size and Shape: As aggregate surface area increases, more cement paste is needed to cover the entire surface of aggregates. So, mixes with smaller aggregates are less workable compared to larger-size aggregates. Elongated, angular, and flaky aggregates are difficult to mix and place and have a greater surface area to cover, decreasing workability. Rounded aggregates have a lower surface area but lack the angularity to develop sufficient bond strengths with the cement paste. Crushed aggregate with the proper proportions provides a better bond with the cement matrix and adequate workability.
- Admixtures: Many types of admixtures alter the workability of fresh concrete, either by design or as a side effect. Surfactants such as superplasticizers reduce attraction between cement and aggregate particles, allowing mixes that can be flowable without too much water's negative strength and segregation effects. Air entraining admixtures for freeze/thaw durability produce air bubbles within a controlled size that can make for easier finishing, although using too much produces a sticky mix with the opposite effect.
Introduction of the Slump Cone
This brings us to what is by far the most popular (some say overused) measure of workability. The slump test was introduced in 1918 by Duff Abrams, a prolific American civil engineer, and concrete researcher, as part of his work defining the effects of the water/cement ratio on concrete strength. The test is performed with the slump cone, originally called the Abrams cone, and provides a qualitative measurement of workability but not a direct indication of the water/cement ratio.
For the ASTM C143 and AASHTO T 119 slump test, A Slump Cone is placed on a solid, level base and filled with fresh concrete in three equal layers rodded in a specified manner to consolidate. The concrete is struck even with the top of the cone, and the cone is carefully lifted straight up and away. The sample then settles or slumps, and the final height is subtracted from the original height of the cone and recorded.
Slumps of 4 to 6 inches (100 to 150mm) are generally considered to be in a desirable range for typical placement and finishing operations, provided they also have suitable w/cm ratios and meet mix design requirements when placed. The form or profile of the slump is also noted and used to judge the reliability of each test:
- True slump - concrete subsides, maintaining its general form
- Shear slump - the top portion of the concrete shears off and slips sideways
- Collapse slump - the concrete collapses completely, likely from the mix being too wet
This concrete slump chart (click to print or download) shows different ranges of slump values and how they might be used.
Tamping rods meeting ASTM/AASHTO standards are required to perform the slump test and accessories like bases, scoops, and more make testing more efficient. Slump cones and accessories are available bundled as Concrete Slump Test Kits for convenience.
K-Slump Tester
Developed in the 1970s by Dr. Karim (Kay) Nasser, a professor at the University of Saskatchewan, the K-Slump tester provides fast, on-the-spot estimates of fresh concrete slump and workability. This device is useful for its portability and convenience and can be deployed for use in areas where a stable setup of a slump cone would be difficult.
A hollow-tube probe with slotted openings is inserted into fresh concrete. As wet concrete flows into the tube, a floating plunger rises to indicate estimated slump values. ASTM C1362 is a withdrawn standard for this method, and a new standard is pending.
What is Self-Consolidating Concrete
Self-consolidating concrete (SCC), also referred to as self-compacting concrete, mixes are designed to be both highly fluid and resistant to segregation, allowing them to flow readily into complex formwork and around congested reinforcing steel with minimum effort. These specialized modern mixes are too fluid to be adequately characterized using the conventional slump test, so new methods have been developed to define their consistency.
Who Invented Self-Compacting Concrete?
The impetus for the development of self-compacting, or self-consolidating, concrete originated in Japan in the mid-1980s. Reduction in a skilled workforce that could properly place and consolidate concrete and increasingly complex formwork and congested reinforcing steel designs seemed set to force an impasse that would prevent the efficient construction of durable concrete structures.
The solution required a new concrete mix design that could flow into the tight corners of formwork and around dense placements of reinforcing steel under its own weight, with no need for vibrating compaction. By 1988, a team of academics and industry professionals led by Professors Okamura and Ozawa at the University of Tokyo developed just such a mix.
Their new approach leveraged supplementary cementitious materials (SCM) such as fly ash, blast furnace slag, and silica fume to produce a material with low viscosity and high resistance to segregation. The first major placement of 180,000yd³ (137,620m³) was for anchor blocks for the Akashi Kaikyo Bridge.
Attracted by the efficiency and reduced cost, Scandinavian countries quickly adopted the technology, developing unique placement procedures and test methods. Other benefits of these free-flowing mixes were noted as well. Placement efficiencies shortened production schedules, and the elimination of vibration greatly reduced the impact of noise in urban areas.
Simplified placement operations increased worker safety. Acceptance and use for these and other types of “high-performance” concretes have spread to Europe and the Americas. Standardized specifications for materials and ASTM test methods ensure reliable and repeatable mix designs for many applications.
SCC Concrete Testing
- Slump Flow Test is measured in ASTM C1611 and AASHTO T 347 methods using a conventional concrete slump cone positioned on a smooth, rigid base plate. The cone can be upright or inverted and filled with concrete in one lift without consolidation. The concrete is allowed to spread after the cone is raised and the amount of spread is measured and reported as the slump flow. If the baseplate is also used to measure concrete flow rate and relative viscosity in the lab, it is required to be marked with two concentric circles.
- J-Ring Test (Passing Ability) is a test described in ASTM C1621 and AASHTO T 345 that gauges how well the concrete mix can flow through closely-spaced reinforcing steel bars. In addition to the slump cone and base plate used in the slump flow test, this method uses a J-Ring test fixture to simulate the rebar placement. As with the flow test, the cone may be placed in either the upright or inverted position within the J-Ring. If the upright position (method A) is opted for, a modified slump cone with the foot tabs removed must be used to avoid interference with the J-Ring fixture. A complete J-Ring test set is available with all required components to perform both the slump flow and J-Ring tests.
- The L-box Test is an alternative method for characterizing the flow and passing ability of SCC mixes. A vertical hopper is filled with concrete and released to a horizontal trough by raising a sliding gate. The concrete then flows past simulated reinforcing bars, and its depth in the trough is measured in two places. This test is in use in Europe and by some state Departments of Transportation but does not currently have an ASTM test method developed.
We hope this blog post on concrete workability and its related test methods has been helpful. If you have questions about any type of construction materials testing, contact the testing experts at Gilson today.
Testing Resources
Standard Test Methods, Specifications, and Practices
Individual test methods and specifications referenced in our product descriptions, blog articles, and videos are available for review or purchase from the professional organizations noted.
- ASTM International (American Society for Testing and Materials)
- AASHTO (American Association of State Highway and Transportation Officials)
- ACI (American Concrete Institute)
- State DOTs (Departments of Transportation)
- ISO (International Organization for Standardization)
- BS (British Standards)
- EN (European Standards)