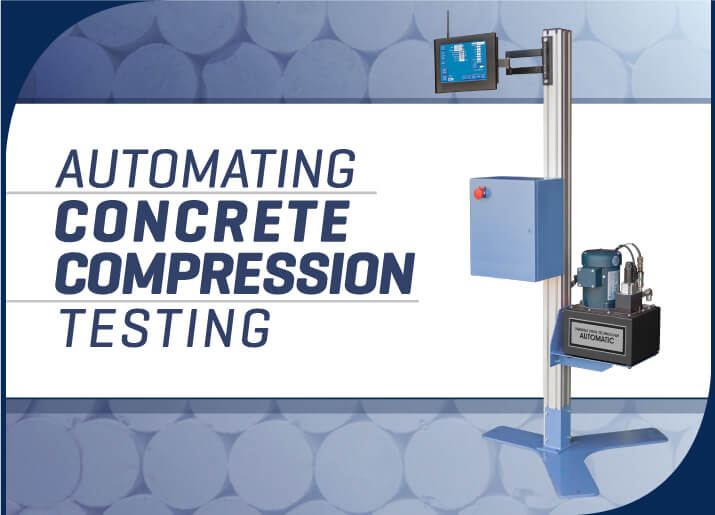
Modern automated concrete compression testing machines evolved naturally from the nexus of digital machine controls, laboratory information management systems (LIMS), and cloud-based software and communication technology.
Basic, or manual, concrete testing machines from reputable manufacturers have reached their apex in accuracy, performance, and features. However, inadvertent human errors, gaps in compliance with test protocols, or inefficient testing practices persist in concrete strength testing programs, frustrating the best intentions to produce accurate, reliable results.
Challenges with Manually Controlled Compression Machines
An experienced technical staff minimizes quality control issues, but even the best and brightest specialists can fall victim to simple errors or inconsistencies. Tasking competent technicians with basic and repetitive tasks is an expensive strategy that does not challenge them or optimize their earning potential. On the other hand, leaving the task of breaking cylinders to entry-level employees risks poor test results and does little to build their technical skills. So, logically, automation is the best way forward to an efficient, high-quality concrete strength testing program.
For testing laboratories contemplating the purchase of a new compression machine for strength testing, there is a lot of incentive to consider a fully outfitted automatic concrete compression machine. The increased efficiency of these devices, their improved accuracy, and reduced human input errors are significant features, and they are built around load frames with proven reliability.
Still, a well-maintained and calibrated manual machine can be accurate, reliable, and meet all the requirements of ASTM C39, even if it was not originally engineered to take advantage of automation technology. For labs with a basic compression machine in good condition, Gilson's Automatic Controller Retrofit series offers a path to full automation and a way to keep pace in a competitive market.
Benefits of Automatic Operation
Our Automatic Controller Retrofit kits convert most basic compression machines to automatic operation by replacing the existing hydraulic and display interface connections. Models for single or dual-load frame machines are offered, with available configurations for modulus of elasticity (MOE) and Poisson's ratio testing.
Retrofit models feature the same human-machine interface (HMI) controllers and hydraulic drive units used for Gilson's Automatic Compression Machines. The kits are shipped preassembled and ready for installation. Basic Compression Machines converted to this system have the same operational features and functionality as our automatic machines.
The HMI controller precisely controls the integrated, variable-speed electric motor and hydraulic pump, regulating the load rates and test cycles of the compression machine for compressive, flexural, and tensile splitting tests on concrete cylinders, cubes, beams, and cores. Specimen failure points and ultimate strength values are automatically detected and recorded.
The unique energy-efficient variable speed loading system regulates load rate and application. The integrated operation of the motor and hydraulic pump is governed by input based on the standard test method selected and feedback from the load sensors. The system is quiet and offers a longer service life for the hydraulic components.
Specimen contact, preloading, load rate, break detection, data acquisition, and piston return to the home position are all performed in complete compliance with ASTM/AASHTO standard test methods. The controller eliminates load rate and preloading variations, ensuring test results' accuracy and repeatability. Data ports and Wi-Fi connectivity optimize information management and integration with user PCs or networks for reporting.
Quick and Easy to Install
After uncrating, the HMI touchscreen display is mounted to its bracket on the aluminum support column and connected to power and data cables from the Retrofit electronic drive unit. Additional connections may be required to operate modulus of elasticity circuits, over-travel limit switches, and other electronic sensors used on the original compression machine.
The hydraulic line from the Retrofit unit is connected to the loading ram of the compression machine, and if needed, hydraulic fluid is added to the Retrofit reservoir. Retrofit models that control dual load frames require additional electronic and hydraulic connections. After removing air from the lines and checking for proper operation, the converted concrete compression machine is ready for calibration and to be put into service.
Note: The Retrofit unit is partly assembled and fully calibrated before leaving the factory. ASTM C39 states that compression machines must be calibrated on-site after relocation or servicing of the loading system. Gilson can provide a list of qualified calibration service providers in your area. |
Concrete Testing and Information Management
Simply putting an automatic compression machine to work in the laboratory improves testing accuracy, consistency, and efficiency, but the benefits do not end there. Automation's full value is realized when an automated compression machine is integrated with a complete concrete information management system.
Gilson Guardian Cloud Sharing Application is a secure information system that collects and shares concrete inspection and test data from the time strength specimens are cast in the field through the distribution of final test reports. The three-part cloud-based system includes a mobile app for field operations, laboratory software that integrates with Gilson Automatic Compression Machines and Automatic Controller Retrofits, and a cloud-based information platform for sharing sample data and test results with project stakeholders.
The mobile app records batch data and fresh concrete properties at the project site when strength specimens are molded. Samples stored for the initial curing phase are geolocated with the app for easy pickup and transport.
Once back in the lab, the specimens are labeled with QR codes for tracking through the final curing, end preparation, and strength testing phases. Test results from the automatic compression machines are logged into the Guardian system and prepared for sending to the cloud. After review and approval, clients, contractors, or other authorized parties can review the sample status and complete reports immediately.
We hope this article has highlighted the benefits of automated concrete testing and explained some options. Please contact our testing experts for questions or help with your application.