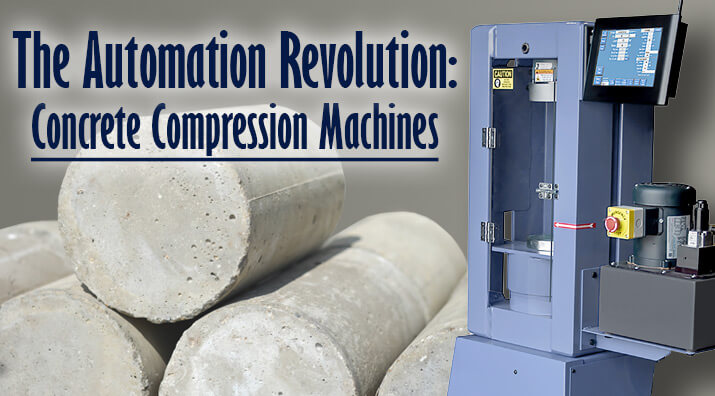
By the early 1900s, when many concrete strength testing methods were standardized, it was clear that the most useful form of concrete strength evaluation was the compressive strength test, usually performed on a cube or cylindrical specimen. For concrete elements subject to bending loads, special fixtures adapted compression machines for flexural testing of rectangular beams to determine the modulus of rupture.
Before hydraulic systems became advanced enough for accurate control of load application, stress rates were manually controlled using stopwatches, and accurate readings of peak load depended on how well you could read the needle of a dial gauge as it paused, vibrated a little, then dropped off during failure.
Maximum readings were manually recorded by pencil on a clipboard. Strength test results were calculated by hand, looked up on a chart, or performed on a slide rule, then recorded in a logbook. Daily test reports were typed up in the front office and sent out in the afternoon mail, and the client could review them two or three days later.Breaking a concrete test cylinder for compressive strength or a concrete beam for flexural strength are straightforward tests. Still, each step in the repetitious process must be performed correctly to produce accurate results. The job often falls to inexperienced technicians with varying motivation levels, and the more specimens there are, the more repetitive and boring the daily process becomes for them. It is not hard to see the potential for compromised test results.
The introduction of electronic/digital testing systems greatly reduced recording errors and streamlined the reporting process. Still, accuracy and repeatability variations caused by manual control of loading and load rates, as well as inconsistencies between individual operators have not been resolved by standard controller units.
Problems with Manual Test Control
A typical compressive strength test for a concrete cylinder takes only a few minutes, but much of that time is spent watching the compression machine and guiding it through the test procedure.
The test method permits the application of the first half of the estimated peak load at a higher speed before completing the test at the specified rate. So, the operator observes the initial load until it reaches their estimation of the halfway point, before manually engaging the machine's hydraulic regulation system for the remainder of the test.
A smooth and consistent changeover from the initial to the final loading rate ensures consistent accuracy and repeatability. For tests where two or more specimens are averaged for a final result, the changeover must occur at the same load point to ensure minimal deviations in reported strength. Even the same operator doesn’t make the changeover at exactly the same point each time. Since tolerances allow a range of loading rates, multiple operators or laboratories can operate within test method requirements, yet still produce inconsistent results.
The technician must then monitor the final stage of testing to document the peak load before failure. If the operator is a bit slow in releasing the load, the test sample may shatter, creating a potential for injury, or at least making a mess to be cleaned up.
There are other concerns when depending upon human response to regulate complex test sequences. Loads must be applied smoothly and without shock. Load gauges need to be watched constantly in case of an unexpected sample failure. Load values must be read properly and manually recorded. When reading analog dial gauges, the operator must be aware of the effects of parallax.
Strategies for Accuracy and Efficiency
Studies show that a final load rate faster than the specified range of 35 ±7psi/second (0.25 ±0.25MPa/second) yields strength values an average of 2.2% too high. So, the actual strength of a concrete cylinder with a 5,000psi test result might be 4,890psi, or even lower if the load rate is too high. Conversely, speeds slower than those specified would produce an artificially low test result. In fact, if a load of around 75% of its ultimate strength is applied to and sustained on the concrete cylinder, it will eventually fail.
Plenty of technicians perform concrete strength tests in construction materials labs every day and successfully produce results within acceptable tolerances, but could these tests be more accurate and repeatable? Could operators be testing more samples in less time? In a busy lab with many samples, one or two technicians might spend several hours just testing concrete cylinders. It's clear that a couple of minutes spent preparing the next specimen for testing or completing a notation on the previous test rather than watching a gauge would save a significant amount of time.
As noted in this previous Gilson blog post, Concrete Cylinder Testing - Field to the Lab, concrete strength test specimens' accurate and meaningful test results depend on following standard practices for sampling and molding, initial and final curing, and handling. A properly executed laboratory test is the final step in producing valuable data that reflects the quality of the material.
Complying with ASTM and AASHTO test methods when testing concrete specimens for compressive, flexural, and tensile strength or elastic properties ensures reasonably accurate results. Many of the constraints for application and control of loading speeds and detection of peak loads depend upon human input, monitoring, and judgment. The tolerance of standardized test methods must accommodate a variety of compression machines currently available, including some with mechanisms and controls that may respond slowly to input and be awkward to regulate.
Automated Control: Sharpening the Point
Automated concrete compression machines feature control systems to regulate loading, load rates, and break detection, resulting in increased accuracy, repeatability, and time savings. The operator selects the desired ASTM/AASHTO test procedure from the menu and inputs the requested specimen data. All that is left is to position the specimen on the platen or in the fixture and check alignment before activating the test cycle. At test completion, the sample is removed and replaced with another for the next cycle. The technician is free to use their time to complete notes and observations, prepare subsequent samples, or perform other tasks.
Advanced machine controllers, programmed with requirements for ASTM C469 modulus of elasticity or Poisson’s ratio testing, are available to complete the entire test cycle following the standard test methods. Load and deformation sensors are purchased separately.
Reduced human intervention to observe and control the testing machine translates to a significant reduction in operator error. The benefits to laboratory quality control are clear-cut and immediate:
- Full compliance with standard test methods is assured
- Consistently accurate test results and enhanced repeatability improve laboratory statistics
- Error-free data is collected for report printout or uploading to computers
- Built-in diagnostic functions indicate fault conditions that must be resolved before testing can proceed
- Sample throughput is increased for maximum efficiency
Testing data complete with sample ID, test results, and machine settings, along with laboratory and client information is collected in real time and stored for uploading to a PC, network, or transfer to a USB flash drive. A printer can be directly attached for an immediate printout of individual tests or summaries.
Gilson Guardian: Total Information Management and Sharing
Gilson Automatic compression machines optimize the flow of specimen data and testing information, making them ideal for integration with our Guardian Cloud-Sharing Application. Gilson Guardian is a secure information management system used to document, report, and distribute concrete inspection and testing information. Click here for a virtual product tour of the Gilson Guardian Application.
Using a mobile app at the jobsite, information on batching data and fresh concrete tests is uploaded to the cloud. When strength specimens are molded and stored for initial curing, the exact position of the sample set is geolocated for easy pickup by the testing lab.
Samples are logged in at the lab and labeled with QR codes indicating mix data, testing dates, and test types. Label information is uploaded to the compression machine controller when scanned, ensuring that the correct standard test method is performed, and test results are recorded properly.
Project stakeholders can stay informed in real time by simply logging into the secure cloud-based website to review current data. The Guardian application instantly shares the status of concrete tests with authorized stakeholders.
Adaptability for the Full Range of Concrete Strength Tests
Like conventional compression machines, automated machines come in a standard configuration ready for ASTM C39 and AASHTO T 22 compressive strength testing of concrete cylinders. A variety of optional fixtures and accessories are available to perform other tests:
- Flexural strength, the tensile or bending strength of concrete, is an important design consideration for pavements, airport runways, and structural elements. Concrete specimens molded in rectangular prisms (beams) are typically tested for flexural strength in compression machines. A unique flexural strength fixture supports the concrete beam on each end and applies a vertical load to either two points at 1/3 the total distance from the ends (ASTM C78/AASHTO T 97 third-point loading) or at one point in the center (ASTM C293/AASHTO T 177).
- Splitting tensile strength is used to evaluate the shear resistance of lightweight concrete in structural elements. In the ASTM C496 or AASHTO T 198 test methods, A concrete cylinder is positioned horizontally on the bottom platen of the compression machine. A compressive load is applied along its length through a tensile splitting bar mounted on the top of the machine.
- Cube specimens are used for concrete compressive strength testing instead of concrete test cylinders in some European standards. Smaller cubes are commonly used to test grout, mortar, or sulfur capping compound specimens with test methods similar to ASTM C109 or AASHTO T 106. Cube Test Sets for 6in/150mm or 2in/50mm cubes include spherically seated upper platens for correct load application and spacers or pedestals for vertical positioning of the specimen in the compression machine.
- Modulus of Elasticity (MOE) and Poisson's Ratio tests characterize the elastic properties of concrete under load. For MOE, a compressometer fixture is positioned on a concrete cylinder for precise deformation and strain measurements while loading. A compressometer/extensometer also measures the horizontal extension of the loaded cylinder to determine Poisson's ratio. Standard test methods for both procedures are described in ASTM C469.
We hope this blog post has helped you understand the benefits of automatic concrete compression testing machines. Please contact our testing experts to discuss the automatic compression machines or retrofitting standard testing machines.
Testing Resources
Standard Test Methods, Specifications, and Practices
Individual test methods and specifications referenced in our product descriptions, blog articles, and videos are available for review or purchase from the professional organizations noted.
- ASTM International (American Society for Testing and Materials)
- AASHTO (American Association of State Highway and Transportation Officials)
- ACI (American Concrete Institute)
- State DOTs (Departments of Transportation)
- ISO (International Organization for Standardization)
- BS (British Standards)
- EN (European Standards)