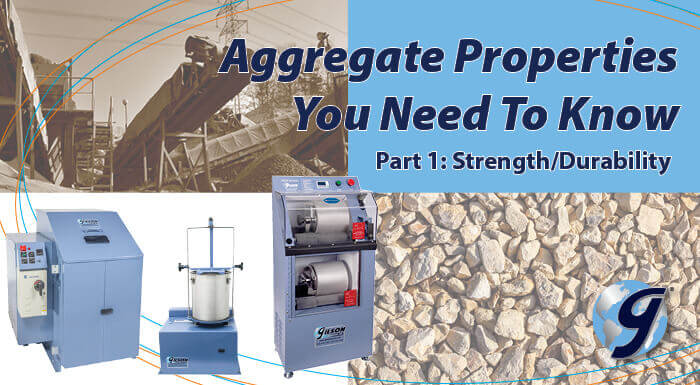
Construction aggregates are mineral materials used in the production of construction materials such as Portland cement concrete and hot-mix asphalt, and as unbound base courses for pavements. In their primary role as filler in these materials, the volume of aggregates can take up 90 – 95% of asphalt and 70 – 80% of concrete mixtures.
However, the function of aggregates in the composite materials goes well beyond that of just filler. Aggregate surface textures can increase the skid resistance of asphalt pavements, and large particle sizes can increase its ultimate load capacity. Sharp, angular aggregate textures can lend certain strength characteristics to concrete, or more rounded shapes can help it flow into confined spaces during placement. Aggregates have a direct and significant impact on the strength, workability, and durability of concrete and asphalt materials, and even the final appearance of structures and pavements.
Production and Resources
Construction aggregates are extracted from natural sand and gravel deposits or quarried from rock formations. The raw, mined materials are crushed to suitable sizes if required, then sorted by size and shape for use as fine or coarse fractions. These mining operations produce some 2.5 billion tons of construction aggregates annually for the U.S. domestic market. Manufactured aggregates are a separate source of materials derived from the waste products (slag) of industrial iron and steel production and from the recycling of concrete. Low-density aggregates used in the production of lightweight concrete come from manufactured sources. These resources go into the production of concrete aggregates, asphalt aggregates, and base course materials for every commercial, industrial, and infrastructure project built.
Testing for Toughness
In this blog, we’ll focus on construction materials tests that measure aggregate characteristics like soundness, toughness, and durability. The size, shape, density, and texture of construction aggregates are just as important and will be addressed in the next blog of this two-part series. To be effective, aggregates must have substantial physical properties to stand up to both external and internal physical forces. They need to be tough and hard to resist abrasive wear and transfer loads, as well as sound and dense to resist degradation and disintegration from freeze-thaw cycles and the manufacturing process. So, a good aggregate must be at least hard, dense, strong, and free of soft, porous, or friable particles.
The most important physical characteristics of good aggregates are all interrelated, but can be better understood by defining a few key terms:
- Toughness: How well the material can absorb energy and resist fracturing when force is applied. Toughness requires a balance of strength and ductility, which allows a material to deform before fracturing.
- Durability: Resistance to internal forces resulting from freezing and thawing or wetting and drying cycles, as well as physical wear. This resistance comes from both density (fewer cracks and voids) and strength. Expansive forces generated in voids and fissures can be tremendous and lead to the disintegration of aggregate particles. Chemical durability problems can result from various forms of cement-aggregate (alkali-silica) reactivity or ASR.
- Soundness: Aggregates with fewer voids, higher strength, and lower absorption resist degradation and disintegration from weathering and internal/external loads.
- Abrasion resistance: A function of hardness and required in both the manufacturing and service-life phases of an aggregate. Good abrasion resistance also helps maintain the skid resistance needed for pavement mixtures.
Selecting Methods and Equipment
Los Angeles (LA) Abrasion Test
Is a widely used procedure that has been around for many years and produces values that are well understood. Dry coarse aggregate samples are rotated in a large steel drum with an abrasive charge of steel balls. A hardened steel shelf lifts the sample and abrasive charge and drops them against the opposite side of the drum as it rotates, creating an impact-crushing effect. Grinding and abrasion continue as the contents roll in the drum. The sample mass retained on a specified sieve size is compared to the total mass of the original sample. Degradation of the aggregates by both abrasion and impact forces is measured and toughness is evaluated. The Los Angeles Abrasion Machine is relatively large, and the test procedure is known for being “robust” and noisy. Separate test methods for small-size and large-size coarse aggregates are described in ASTM C131 and C535. AASHTO T 96 method for small-size coarse aggregate is similar to C131. For further information regarding this test, read our blog post L.A. Abrasion Test: Aggregate Abrasion Testing.
Micro-Deval Test
Is an abrasion loss test carried out on fine or coarse aggregate samples that are partially submerged in water. The Micro-Deval Apparatus is essentially a ball mill using stainless steel jars positioned on a roller mechanism. Samples, with water and an abrasive charge of steel balls, are placed in the jars and then rotated for a prescribed time at a specified speed. The samples and the ball charge are considerably smaller than those used in the LA abrasion methods and are not subjected to significant impact forces. The results of the test are more focused on durability and abrasion resistance. ASTM methods for testing coarse and fine aggregates are found in D6928 and D7428. Other variations of the test occur with AASHTO T 327, Texas DOT Tex-461-Aon, and Ontario LS-618. The popularity of the Micro-Deval test has increased in recent years because of its accuracy and repeatability, as well as convenience and the smaller scale of the apparatus. European test standard EN 1097-1 refers to an unrelated Micro-Deval apparatus that is substantially different than the one described here. For further information regarding this test, read our blog post Micro-Deval Test Method - Aggregate Abrasion Testing.
Sulfate Soundness Test
Is a cyclical test that evaluates aggregates for durability and resistance to degradation from freeze-thaw cycles. Coarse or fine aggregate samples are repeatedly immersed in a saturated sodium or magnesium sulfate solution and oven-dried between cycles. Salt crystals growing in micro-fissures of the aggregate simulate the expansive forces of ice crystals throughout the cycles, and loss in mass is determined for different sieve size fractions as the particles degrade. This is a popular test for the initial evaluation of an aggregate source, but the required cycles can take several days to complete and repeatability is poor. There are variations in the apparatus for sulfate soundness testing, and a number of components are purchased as needed to carry out the test method in ASTM C88 or AASHTO T 104. AASHTO T 103 is an alternate test method utilizing a similar procedure using water or weak ethyl-alcohol solution in actual freezing temperatures. For further information regarding this test, read our blog post Sulfate Soundness Test of Aggregates - Estimating Durability.
Durability Index Test
Is an abrasion loss test that looks specifically at the production of clay-like fines as an aggregate sample degrades. These fines are known to be detrimental to asphalt mixtures. The test is also used to determine the suitability of aggregates for use in bases, backfill, and riprap. For the test method in ASTM D3744 and AASHTO T 210, the sample is agitated with water in a stainless steel wash vessel on a Durability Index Agitator with a lateral reciprocating action. At completion, a modified sand equivalent test is performed on the minus 75µm (#200) fines fraction. This test is most often used in western states to identify aggregates unsuitable for use in asphalt mixtures and unbound pavement bases.
Accelerated Polishing Test
Simulates the action of car and truck tires on the coarse aggregates used in asphalt pavement mixtures. Selected aggregate pieces are embedded in a circular “road wheel” test fixture, then brought into contact with a loaded, rotating rubber tire. The Accelerated Polishing Machine provides a polish value to classify the aggregates for their skid resistance. The test method, including the use of alternate testing tires, is described in ASTM D3319 and AASHTO T 279, as well as some European standards.
Slake Durability Test
Is a qualitative test for softer/weaker rocks such as shale, so it is not often used to test aggregates under consideration for concrete or asphalt mix designs. It is useful for evaluating these materials for unbound pavement base courses or structural and embankment fill applications. The Slake Durability Apparatus consists of two wire mesh drums that rotate the test specimen through a water-filled trough. The samples are then oven-dried and, after two cycles, the mass retained is determined and compared to the original mass. The test is defined in ASTM D4644, and values show the tendency of the material to weaken and disintegrate under weathering conditions.
We hope this blog post on Properties of Aggregates has been helpful. Please contact our testing experts to discuss your application.
Testing Resources
Standard Test Methods, Specifications, and Practices
Individual test methods and specifications referenced in our product descriptions, blog articles, and videos are available for review or purchase from the professional organizations noted.
- ASTM International (American Society for Testing and Materials)
- AASHTO (American Association of State Highway and Transportation Officials)
- ACI (American Concrete Institute)
- State DOTs (Departments of Transportation)
- ISO (International Organization for Standardization)
- BS (British Standards)
- EN (European Standards)