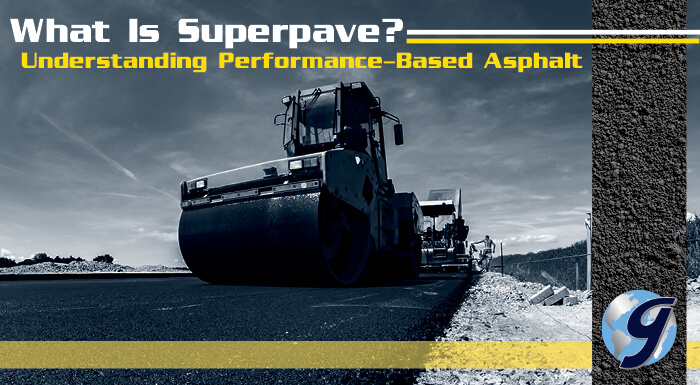
What is Superpave?
The term "Superpave" is an acronym for Superior Performing Asphalt Pavements, which evolved from partnerships created among the Federal Highway Administration (FHWA), American Association of State Highway, and Transportation Officials (AASHTO), TRB, and others in the SHRP community.
Congress provided additional funding for this and other transportation-related programs in 1991 through the Intermodal Surface Transportation Efficiency Act (ISTEA). As with many large-scale programs at the federal level, its origins came from simple questions and ballooned into complex and numerous offshoots as time passed and funding permitted. In this blog post, we’ll discuss the impact of Superpave from the perspective of mix design, construction materials testing, and resources for laboratory equipment.
Superpave Mix Design
Superpave is an asphalt mix design method that has its roots in a report released back in 1984 by the Transportation Research Board (TRB), America's Highways, Accelerating the Search for Innovation. The report outlined the need for increased state and federal funds to develop badly needed research for better and longer-lasting highways. In response, Congress authorized funds in 1987 for the Strategic Highway Research Program (SHRP), a five-year program to evaluate and develop ways to improve the durability and efficiency of asphalt and concrete pavements, concrete structures, safety, and overall performance of America’s highways.
A New Approach to Asphalt Mix Design
Rather than a specific process or procedure, Superpave is a performance-based specification for asphalt binder and volumetric mixture design. The idea was to allow asphalt pavement designs that could handle the unique weather and traffic conditions of a given site in any geographic area of the U.S. The system consisted of three components:
- Asphalt binder specification. A system of classifying asphalt binder based on its performance response to temperatures and aging characteristics
- A design system grounded in traffic loading and environmental conditions
- Mix design system and analysis tests for performance prediction models
Superpave leverages modern asphalt paving technology to develop mixtures more resistant to cracking from low temperature and fatigue factors and reduce permanent deformation. Superpave means mix designs can be tailored for better performance and longer life based on a geographical area’s temperature extremes, traffic loads, and utilization of the road or highway.
Superpave vs. Marshall
Compared to the Marshall design method, Superpave integrates material selection and mix design and uses an entirely different type of compaction. Instead of the impact of weighted hammer blows, the Superpave gyratory compactor (SGC) uses a hydraulically powered kneading system with an action much closer to the actual field densification of the mix. The applied force is constant, the number of gyrations can be controlled, and the device produces feedback on the compactibility of the asphalt material. Optimum densities developed with the SGC often require less asphalt binder than Marshall methods.
A 2002 article, Superpave Comes of Age, in Public Roads magazine, points out that Superpave is not a one-size-fits-all solution. For instance, a mix design for pavement in the Nevada desert with warm temperatures and light traffic would not fare well on a frigid, highly traveled metropolitan Minnesota city road. The article also refers to Superpave as a “complex system of choices,” noting that new and different tests are required for the classification and selection of binder and aggregate.
The first step in the design process is a collection of the environmental and usage information for the project. In other words, maximum/minimum temperatures for both air and pavement, along with current and anticipated traffic types and loads. Testing and selection criteria for PG binder, combined aggregate requirements, and mixture design are detailed in AASHTO M 323.
Asphalt Binder Performance Grades (PG)
Superpave asphalt binder performance grade (PG) designations are related to the average seven-day and minimum anticipated pavement design temperatures, and the designations directly state these temperatures. A PG 64-16 binder is for use at a project site where the average seven-day maximum pavement temperature is 64°C, and the expected minimum pavement temperature is -16°C.
A series of tests listed in AASHTO M 320 characterize the binder and its suitability for given environmental conditions. Some of the tests are not new but are now performed over a wider range of temperatures more directly related to field performance, and both short and long-term aging is considered. These tests are more effective in examining the properties that lead to thermal and fatigue cracking, as well as rutting.
AASHTO | ASTM | Test Description | Testing Equipment |
---|---|---|---|
T 48 | D92 | Flash Point | Cleveland Open Cup Tester |
T 240 | D2872 | Rolling Thin-Film Oven | RTFO Ovens |
T 313 | D6648 | Flexural Creep Stiffness | Bending Beam Rheometers (BBR) |
T 314 | - | Direct Tension Test | - |
T 315 | D7175 | Dynamic Shear | Dynamic Shear Rheometers |
T 316 | D4402 | Rotational Viscosity | Rotational Viscometers |
R 28 | D6521 | Accelerated Aging | Pressure Aging Vessel (PAV) Vacuum Degassing Oven (VDO) |
Aggregate Selection
Aggregates make up about 95% of an asphalt mixture, and their function in the overall performance of a pavement is critical. Superpave has unique criteria for aggregate acceptability that are detailed in section 6 of AASHTO M 323. Because aggregates from a single source rarely meet all the requirements, materials from different stockpiles are frequently blended to produce an acceptable mix design.
- Gradation control points mean that the percentage passing values of the gradation curve must fall between the specified points. Aggregate gradation tests are performed using standard methods (AASHTO T 27 / ASTM C136) and equipment (AASHTO M 92 / ASTM E11 test sieves). Gradation directly affects pavement performance factors like strength, stability, permeability, and fatigue resistance. Maximum size is also a factor in lift thickness and compaction.
- Consensus property requirements specify fine aggregate angularity, percentage of fracture faces, and sand equivalent (clay content) values as well as shape. Angular aggregates resist rutting due to their greater shear resistance, but they also tend to form higher aggregate air voids, a problem when trying to control the amount of binder used. Superpave aggregate consensus properties are based on anticipated equivalent single-axle loads (ESALs) and depth from the surface.
- Source properties are the third criteria not covered in M 323 but are often used when more traditional tests for durability and soundness are required locally.
AASHTO | ASTM | Test Description | Testing Equipment |
---|---|---|---|
T 304 | C1252 | Void Content of Fine Aggregate | Fine Aggregate Angularity Apparatus |
T 335 | - | Percentage of Fractured Faces¹ | - |
- | D4791 (withdrawn) | Flat and Elongated Particles | Proportional Calipers |
T 176 | D2419 | Sand Equivalent Value | Sand Equivalent Apparatus |
¹ is a visual evaluation of fracture surfaces on separated size fractions of aggregate |
Superpave Mix Design Analysis
Once local environmental conditions have been collected to determine which PG asphalt binder to use and an aggregate blend has been selected, it’s time to establish the optimum binder content. Several trial mixes are prepared, two at the proposed binder content and two at 0.5% higher and 0.5% lower.
Each trial mix sample is compacted in the Superpave gyratory compactor using three different gyration cycles based on 20-year traffic loading estimates in millions of ESALs from AASHTO R 35:
- Ninitial: This number of gyrations measures compactibility of the mix during construction. If mixture air voids are too low at this point, the pavement may be unstable under traffic loads. This may also be an indication of too much natural sand in the mixture.
- Ndesign: The number of gyrations to duplicate the expected density of the mixture in the field. An air void content of 4% is ideal at this point.
- Nmax: This number of gyrations produces a density that should not be exceeded in the field. Air voids less than about 2% at Nmax result in a mix that compacts too much under traffic and is susceptible to rutting.
After testing in the gyratory compactor, separate samples of each trial mix undergo maximum and bulk-specific gravity testing. Test values from the theoretical maximum specific gravity (Gmm or Rice test) and bulk specific gravity tests (Gmb) are used to calculate air void content (Va) and voids in mineral aggregates (Vma) values.
AASHTO | ASTM | Test Description | Testing Equipment |
---|---|---|---|
T 312 | D6925¹ | Gyratory Compaction | Superpave Gyratory Compactors |
T 209 | - | Theoretical Max Specific Gravity | Asphalt Maximum Specific Gravity |
T 166 | - | Asphalt Bulk Specific Gravity (SSD) | Specific Gravity Accessories |
T 275 | - | Asphalt Bulk Specific Gravity (Paraffin Coated) | Specific Gravity Accessories |
¹ASTM D6925 uses a process different than Superpave for this test method |
We hope this blog post has answered your questions about the Superpave and the Superpave asphalt mix design process. If you have questions about your particular applications, contact our testing experts for help.
Additional Resources
Superpave continues to grow and evolve as a design method. These links are great sources of information for the background, history, development, and advancement of the practice.
- America’s Highways: Accelerating the Search for Innovation, TRB Special Report No. 202 (1984)
- The Strategic Highway Research Program: An Investment That Has Paid Off, Public Roads Article (1998)
- Superpave Comes of Age, Public Roads Article, (2002)
- Final Report of the TRB Superpave Committee, TRB Publication (2005)
- Superpave Mix Design and Gyratory Compaction Levels, Tech Brief from FHWA
- Development in Asphalt Binder Specifications, TRB Circular E-C147 (2010)
- The Superpave Mix Design System: Anatomy of a Research Program, NCHRP Web-Only Document 186 (2012)
- Refining Superpave Asphalt Binder Characterization, Asphalt Magazine, (2012)
- Superpave for Construction, National Highway Institute & FHWA Training Course, (2019)
Testing Resources
Standard Test Methods, Specifications, and Practices
Individual test methods and specifications referenced in our product descriptions, blog articles, and videos are available for review or purchase from the professional organizations noted.
- ASTM International (American Society for Testing and Materials)
- AASHTO (American Association of State Highway and Transportation Officials)
- ACI (American Concrete Institute)
- State DOTs (Departments of Transportation)
- ISO (International Organization for Standardization)
- BS (British Standards)
- EN (European Standards)