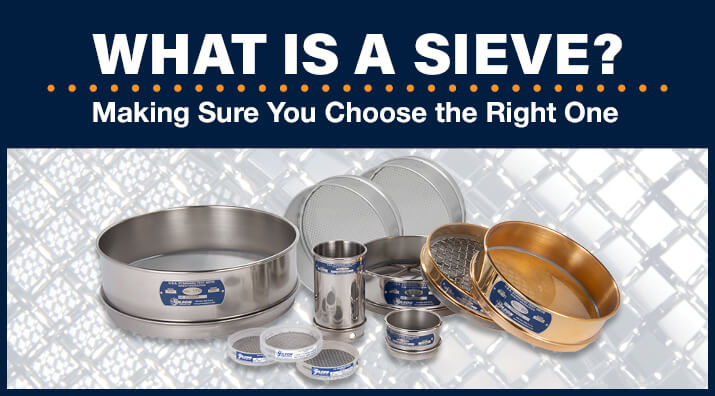
Quick, name the most widely used and cost-effective scientific instrument in your laboratory. Some possibilities come to mind, but our argument is for the ordinary test sieve. By a wide margin, there is no more simple, efficient, or cost-effective way to profile particle dimensions for an extensive range of materials than test sieving.
Sophisticated instruments that take more precise measurements have their place in particle analysis. However, the benefits gained can’t always offset the effort and costs when basic particle sizing and gradations are the focus. These instruments can also confuse traditional interpretations of accumulated historical data if the results do not correlate with mesh sieve testing.
What is the Purpose of Test Sieves?
Sieving is an ancient science based on simple principles deeply rooted in materials testing laboratories as a standard method for measuring particle size. There has always been a question of the absolute accuracy of particle sizing by sieving since the process assumes each particle to be a perfect sphere.
Why Sieving?
It has been practiced for so long on so many different materials that variations in shape for things like construction materials, chemicals, food, pharmaceutical granular material, powders, and many other products are accepted. Each of these disciplines have developed published test methods for their materials. ASTM also publishes their own. The Manual 32 - Test Sieving Methods, is ASTM's comprehensive guide for test sieving methods and analysis procedures.
ASTM E11 and ISO 3310-1 standards list specifications for woven wire sieves. Particles from 150mm (6in) to 5µm (0.0002in) can be sieved effectively using appropriate test methods.
The Standard Sieve
So, while test sieves are quite simple, they are still scientific instruments that should be selected, used, and maintained carefully. Let’s take a closer look at the mesh sieve itself, sieve construction, materials, and design options.
Selecting the Type of Sieve to Fit Your Needs:
Selecting the Separation Media
The separation medium for most sieves is metal or synthetic woven wire mesh. Perforated metal plates are another separation medium, as is electroformed mesh, a flat metallic sheet with precision openings.
For conventional ASTM/ISO test sieves with woven-wire mesh, the range of opening sizes is 125mm to 20µm (5.0in to No.635). It is left to industry-standard test methods, or sometimes the operator, to determine which opening sizes suit a particular sample.
Some test methods dictate the required openings or sieves may be selected to provide useful information on a gradation curve. It is common to use every second or fourth size in the series for an even indication of distribution. An intermediate sieve inserted into the stack can prevent overloading or better define a range of sizes.
Different Types of Sieve Media
Woven-wire mesh is fabricated on large industrial looms in various weave patterns using metal wire. The wire mesh is cut to size and mounted on frames by soldering or with high-strength epoxy adhesives. Proper tensioning ensures uniform openings and prevents finer wire cloth meshes from stretching and sagging during use, increasing the service life of the sieve.
- Brass wire mesh has been favored in the past for sieves because of its malleability and formerly lower cost. It is still sometimes desirable for certain hazardous materials because of their resistance to sparking. The brass mesh is available in sizes from 2.36mm to 45µm (No. 8 to No. 325).
- Stainless steel mesh is much more durable, less likely to contaminate sensitive materials during processing, and maintains its specified openings better. These days, it also features lower cost than brass, and modern tooling makes it easier to weave, form, and mount. Stainless steel mesh is available in the full range of ASTM/ISO sizes from 125mm to 20µm (5.0in to No.635).
Non-metallic mesh woven from polyester or nylon filament is available for non-metallic sieves for unique applications or as a disposable cloth for use in two-part sieve frames. This synthetic mesh is useful for applications where the metal mesh is not permissible or may become contaminated. Opening sizes are equivalent to many ASTM/ISO sizes, but synthetic cloth does not meet E11 or 3310-1 requirements for the material type or wire diameter.
Perforated plate is a precision-punched steel plate meeting requirements of ASTM E323. Perforated plate is often used for the sieve analysis of coal (ASTM D4749), or ores, coke, wood chips, and other special materials. Perforated plate openings range from 3.18 to 100mm (1/8 to 4.0in).
Electroformed mesh opening sizes are square, highly accurate, and very consistent. Tolerances are held to ±1 to 2µm for openings from 150µm to 5µm. This sieving media is expensive, and the fine mesh can be fragile, but it is the optimum choice for applications where precise sizing of fine materials is critical. Nickel used to manufacture electroformed mesh is electrodeposited on a flat stainless steel grid surface. ASTM E161 and ISO 3310-3 specifications list tolerances for these sieves, and they are individually measured and supplied with documentation of compliance.
Selecting the Frame
Just as opening sizes must be selected based on material size, consider the frame type when choosing sieves.
Sieve frames provide a stable platform for proper mounting and tensioning of the sieve mesh and confine the sample material during agitation. Round test sieves include a skirt that enables nesting with other sieves, forming a multi-sieve stack for use in a sieve shaker.
Frames for conventional round test sieves are available in several configurations, and selecting the right one makes a difference for each application. A previous blog post goes into detail about unique frames like Screen trays for Testing Screens, wet-wash sieves, and other sieves for less common applications.
Frame diameter is a crucial step in matching the size of the sieve to the sample volume. Large samples contained within a frame that is too small result in poor separations when particles do not find sieve openings. Size fractions are not entirely separated. A rule of thumb for matching frame diameter to sample volume is that no more than one or two layers of material should remain on a sieve after separation is complete.
Selecting a large sieve allows a larger, more representative sample to be used and promotes better division of fractions. Conversely, smaller sieve frames offer better control over small specimens of fine powders and are easier to clean for the complete recovery of particles. Some test methods recommend test sieves to have a minimum of five full openings, so any sieve has limitations on the upper size of mesh openings.
The chart below lists frame dimensions for ASTM E11 and ISO 3310 test sieves.
Frame height options allow you to maximize testing efficiency when separating multiple fractions on a sieve shaker. Half-height sieves allow a greater number of sieves in a stack in the same vertical space. Bear in mind that during agitation, each particle must have enough room to be lifted off the mesh surface, reorient, then land back on the mesh in a different position, so coarse particles will still require a full-height sieve.
Frame material selection is most often a practical matter of price, long-term durability, and requirements of the application.
- Stainless steel is the optimum choice for most applications for its lower cost, long service life, low rate of sample contamination, and resistance to corrosion.
- Brass has become more expensive recently but is a traditional choice and can still be useful for testing certain materials where sparking could be a concern.
- Combination Frames feature Stainless steel mesh with a brass frame hoop and a stainless-steel skirt for added durability.
- Acrylic frames have certain advantages for smaller sieves. The material is easily machined for a precise nesting fit and allows visual monitoring of the sample during agitation. High-strength adhesives securely anchor the sieve mesh to the frame.
Backing cloth is an option designed to increase the useful life of the primary sieve and offset the effects of frequent use and overloading. The coarser, stronger No. 30 (600µm) wire mesh is factory-installed under the finer primary mesh of No. 70 (212µm) and finer test sieves as reinforcement, especially for wet-wash sieves.
As an industry leader for particle sizing equipment, Gilson is a major resource for useful information on sieves and sieving. Below are links to a selection of videos and previous blogs from our archives that we think are most useful to this series. Please visit our video or blog pages for complete listings.
Helpful Sieve Analysis Resources:
Gilson Videos:
Cumulative vs. Fractional Sieving
Re-Verification of Used Sieves
We hope this blog post has helped you understand the form and function of test sieves. Please contact us with questions about your applications.
Testing Resources
Standard Test Methods, Specifications, and Practices
Individual test methods and specifications referenced in our product descriptions, blog articles, and videos are available for review or purchase from the professional organizations noted.
- ASTM International (American Society for Testing and Materials)
- AASHTO (American Association of State Highway and Transportation Officials)
- ACI (American Concrete Institute)
- State DOTs (Departments of Transportation)
- ISO (International Organization for Standardization)
- BS (British Standards)
- EN (European Standards)